Charles Ross and Son Company
Sales
710 Old Willets PathHauppauge, NY 11788 US
631-234-0500
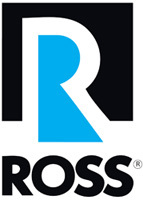
Company Overview
Ross equipment is the first choice for mixers, blenders, dryers and dispersion equipment. The company has a world-class reputation for innovative engineering, superb construction and fast delivery. Ross equipment is manufactured on five continents. In the USA alone, we operate five plants and a vigorous R & D program.