Web-enabled real-time plant information management
Intelligent systems (IS) technologies have received much attention in a wide range of process engineering applications including process operations. The explosive development of Internet technologies has created new opportunities and become a serious challenge to both management and technical teams. Objects and components are changing the way everyone relates to their computer and networks. The impact is also being seen in the manufacturing community, and most people believe that the rate of change will continue to increase.
All information technology systems have data and communications tools for personnel. Companies must have a strategy to leverage information in their manufacturing plants within the supply chain to empower all employees. If accurate information is not available, more inventory must be maintained at both ends of the supply chain. The Industrial Desktop environment allows users to automate decisions, intelligently analyze large amounts of data, and learn from past experiences. Users can adapt their desktop according to their domain knowledge, roles, skills and responsibilities. This strategy enhances collaboration between working groups (Operations, Management, Maintenance, and Engineering).
This paper presents a detailed description of the data hierarchy and new methods to transform data into information/decision required for improving enterprise wide plant operations. The best method to enable active decision-making and collaboration between diverse teams is continuous improvement and innovation fueled by data collection and analysis. Two case studies are presented to demonstrate these emerging technologies.
Contents
Introduction
Business goals
Internet-enabled industrial desktop
ERP challenges
Data unification
Requirements for Web-based information delivery
Analysis of ERP data
Calculations
Manual vs. automatic data entry
E-business
Case study: Polimeri Europa
Case study: Eastman Chemical
Conclusion
Introduction
Companies must have a strategy to utilize the vast information in their manufacturing plants to achieve a competitive advantage. If accurate information is not available, more profit-eating inventory must be maintained at both ends of the supply chain. Large companies have eliminated millions of dollars of inventory by installing real-time links from ERP to plants. This architecture empowers all employees with accurate and current data delivered via a browser in any format they define.
Events at multiple global production facilities directly affect the corporation's business goals. Accurate and timely information exchange between both domains (i.e., real-time at the various plants and transactional at business) is required to meet corporate objectives. For example, ERP needs real-time inventory to calculate ATP (Available-To-Promise) and determine when material will be available to meet a new customer order without pushing existing orders into negative inventory. ERP-certified software products can collect data from hundreds of different systems on the plant floor and translate these values into information expected by ERP. Many ERP vendors today support the technology required to provide flexible viewing of plant floor data. Plant Information Management Systems that deliver real-time and historical data into these ERP containers support analysis of ERP data (recipes, quality inspections, maintenance notifications) with actual process data. These tools are very useful for monitoring process conditions and for displaying ERP data in a consistent, understandable, and visual environment.
Return to Table of Contents
Business goals
Plant/ERP gateways allow engineers and management to leverage production information using Web-based delivery based on real-time plants events:
- Asset Efficiency - operating to capacity and maximizing equipment uptime with timely, condition-based maintenance using operating hours, and alarms (e.g., temperature, vibration)
- Enhance coordination between manufacturing, maintenance and logistics
- Cycle Time - reduce time from order placement to customer delivery
- Increase Profits - plant control systems don't have access to data required to optimize profits like material costs, energy costs, market demand and prices for finished products
- Analyze tradeoffs to satisfy business objectives of reducing operational costs and inventory, improving delivery times, and improving customer service
- Available-To-Promise - provide reliable delivery date to customer based on real-time view of finished goods inventory, production plan, raw materials, etc
- Overcome manual entry problems: slow and error prone, limited volume of data that can be handled
Return to Table of Contents
Internet-enabled industrial desktop
Today, economic information is combined with production data on a monthly, weekly, or at best, on a daily basis. Summary reports at many different "layers of aggregation" are presented to management for decision-making. This type of procedure is manual, tedious, and eliminates the opportunity to react to prevailing economic and plant conditions. Operating staffs do not have timely access to meaningful operating data or the analysis tools essential for sustained performance at peak efficiency.4 Web applications are required to satisfy this goal.
A Web application is much more complex than web publishing. Web publication is trivial to build, but we must recognize that the web is dumb. It's an asynchronous environment providing no connection status, just broadcasting information. Web applications are much more complicated, and they involve a middle tier to marshal information from a database server and present it to client PCs. They must collect data from many complex systems and present it to users in any format they want. OLAP analysis tools are essential to perform analysis by unit, by product, etc. Providing access to only 80% of the data simply won't suffice. Issues to overcome include the magnitude of data (some manufacturing plants have over 100,000 measurements), aggregation of the data (vendors can't assume data usage requirements when designing software products), and data unification. Figure 1 shows an example of a Web application.
The Industrial Desktop is a PC-based platform that is capable of responding to real-time events from manufacturing plants. It allows engineers, operators, maintenance, and management to utilize real-time and historical plant information to detect and solve problems more quickly.1 Sophisticated shrink-wrapped software is used as the basic container for the Industrial Desktop. Microsoft DNA technology is used to integrate information from different sources and present it to the desktop. Microsoft compliant programs exist for word-processing, spreadsheets, electronic mail, mathematical and statistical analysis or simulation programs, but only the Industrial Desktop has real-time events from the plants available for automating its functions.2
The Industrial Desktop supports data shaping. This refers to the creation of parent -> child -> grandchild -> ... relationships between data. There are many reasons that an application might want to create these relationships for plant systems. Process engineers would look at data in the order plant -> area -> unit -> unit operation -> device -> tag. Managers would like to setup a "slice" that compared plant to plant or area to area. Maintenance people could have a totally different view such as plant -> equipment type -> asset -> data and might want to look at all rotating equipment.
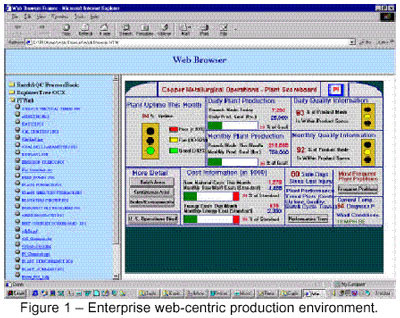
Return to Table of Contents
ERP challenges
According to Gartner Group, "Manufacturing businesses that make investments in ERP-directed manufacturing applications that fail to provide for accurate real-time information from the process will achieve at least 50% lower ROI on those investments..."
It's clear that a connection from ERP to manufacturing plants is desirable. However, linking ERP to the plants is not trivial. ERP systems can't handle direct communication with plant automation systems because of the inherent data volume and various protocols involved. An infrastructure is needed to reliably collect data from all these different systems, "validate" the data, and determine what information should be delivered to the ERP system.
Once the plants are visible to ERP, employees can access the information via the Internet and Intranet to make better business decisions. For example, assume a plant is unable to produce a material that has suddenly experienced high demand. An analysis could be performed before routing production to another facility. The analysis would determine another plant's ability to deliver efficiency, quality, etc, based on historical production information correlated to ERP quality measurements.
Return to Table of Contents
Data unification
Business decisions are only as good as the data on which they are based, and accurate information is essential to the profitability of a manufacturing company. Companies need to understand what the data means, the quality of the data, and ensure that it balances. Plant data is a critical component of business analysis, but the data is often incorrect. These errors can result from bad measurements, inappropriately sized flow meters, poor calibrations on instruments, faulty calculations, inaccurate lab analysis, etc. Meters with moving parts and orifice plates wear, and they must be rebuilt or re-calibrated on a regular schedule, sometimes as often as every three months. Even when instruments are re-calibrated and put back on line, their accuracy can be impacted if the properties of the material being measured are different than the material used for calibration.
Data Unification software products allow manufacturing plants to analyze the quality of flow and inventory measurements and produce a single consistent set of the most accurate reconciled data possible. Typically, these systems use a statistical least-squares method to crosscheck measurement errors on all meter and gauge readings according to the tolerance assigned to each measurement. An accurate set of data is produced that both the accountants (ERP) and the engineers (plant personnel) can use and believe. When delivering information to all employees via web-based technology, reconciled data should be used to ensure accuracy and reliability.
Return to Table of Contents
Requirements for Web-based information delivery
A fully-integrated Web-based application must enable sharing of all company information worldwide and allow users to deploy built-in sophisticated applications. Company-specific applications allow users to analyze, distribute and report information through a Web browser over the Internet, or through a company's Intranet. This environment empowers corporate-wide users by providing access to both real-time and historical production information. They can also access data-event driven applications, which proactively help analyze and manage cost- and time-critical information.
These systems should deploy using an automated download setup (with version control) allowing worldwide installation from one remote PC. This approach eliminates the need to run individual setups on hundreds of corporate PCs. Once deployed, these products should maintain positive handshaking at all times with the servers to which they are connected. Active handshaking ensures that the client applications will know if the servers did not receive the information, and vice versa. Security features should include a tag-by-tag security system and built-in digital signatures. These signatures help protect valuable corporate information, and they provide proof of authorship and insurance that a virus has not been attached.
Return to Table of Contents
Analysis of ERP data
ERP systems were designed to cost assets—not improve plant performance. Plant/ERP gateways provide tools to graphically analyze ERP transactional data and manufacturing process data. ERP systems have the cost and time duration of orders, but they can't determine why an order cost more or took longer than another order. ERP orders together with the manufacturing conditions (e.g., temperatures, pressures, etc) are required to perform order-to-order comparisons. Also, integrated Plant/ERP data is required to determine if ERP master recipe changes affected product quality. Similarly, an analysis could be performed to correlate quality defects and temperature profiles. Real-time integration between global manufacturing facilities and the corporate ERP system, combined with information delivery via web technology, helps plants detect and solve problems like bottlenecks, malfunctions and environmental non-compliance.
Some chemical companies use Plant/ERP integration to support parametric acceptance of their manufactured products. If the raw materials and manufacturing process are within specs, then the product will not be tested in the lab. The ERP system has the raw material specs based on quality tests performed on received materials. Plant historians have the process history and batch templates used to determine if the product was manufactured within the upper/lower control targets. The batch templates were derived from historical data from "good" batches, and these templates are essentially non-linear product alarms. Plant/ERP gateways enable plant personnel to extract operational data out of the business system. Local queries are served by the gateway (e.g., what plant batches went into this ERP campaign). The results can be displayed in any GUI the user wants, and custom and costly ERP reports are not required.
Return to Table of Contents
Calculations
Plant/ERP gateways must be designed to be flexible for calculations. ERP doesn't want raw data from the plant — it needs calculated data. For example, the quantity of material consumed might be calculated by integrating the flow rate signal from the control system. The gateway should support an intuitive configuration environment with predefined data transformation routines. Here are some typical data transformations that ERP systems need:
- Get difference. The material produced is the difference between the amount at start and end time (e.g., tank levels). A ‘wait' version of this translation method could be used to ensure a manual "tank dip" has taken place before calculating the difference. The volume can be calculated from the level measurement by using strapping tables for the tank.
- Get discrete sum. The material produced is the sum of individual weigh scale measurements (e.g., add all weights from start to end of recipe phase).
Return to Table of Contents
Manual vs. automatic data entry
Plant/ERP gateways provide an automatic interface to transfer production data into ERP. In many cases, plants using ERP are entering data manually. A manual entry process is very slow and error-prone, and the volume of data that can be handled is limited. In addition, manual calculations are often required to determine the correct number that ERP needs. Manual entry impacts the timeliness of data sent to ERP.
Often, plant personnel are unhappy with ERP because it actually increases the amount of work they must do. They need to enter data into the plant control systems and duplicate some of the data entry into ERP. If production problems prevent timely data entry into ERP, month-end close and financial (e.g., cost/unit) calculations can be impacted. Plus, it is difficult to extract information from ERP for meaningful analysis once the data has been manually entered (e.g., yield reporting). Don't turn engineers and operators into data entry clerks. ERP-certified gateways can replace the manual entry and automatically send data (e.g., quantity of material consumed, material produced, lot numbers, etc) to ERP when production is finished or partially finished.
Return to Table of Contents
E-business
The ultimate goal of enterprise computing is complete and accurate back-end to front-end integration. ERP must be notified when manufacturing problems occur since these corporate systems are often a key component of an E-Business strategy . In many cases, without a real-time connection, ERP may only recognize a problem when it's too late (i.e., if product is not shipping). Execution to plan is expected with consistent quality, costs, and schedule. The key is being able to react to unplanned events in manufacturing plants. A software infrastructure is required to capture plant events, transform the raw data into a business context, and expose these business events programmatically to other applications.
As companies deploy their E-Business strategy, greater emphasis will be placed on coordination between manufacturing and sales. Therefore, companies need real-time plant/SAP integration to provide an accurate view of manufacturing to ERP. Once the integration is established, real-time delivery of this information must be enabled in an intuitive user interface (browser). If the software is not easy to use (most ERP screens fall into this category), then companies have lost the competitive advantage that their ERP investment could provide.
The AMR slide in Figure 2 shows how plant events directly affect business. Achieving brand image ultimately translates into reduced variability during manufacturing. Producing to schedule is a key requirement to attain the business goal of increased agility. Manufacturing plants are a key part of the overall supply chain. Flexibility is required to respond to macro level events (new products, changing customer requirements, changing market requirements) and micro level events (production problems, schedule changes, etc). Web technology can combine data from all parts of the supply chain to provide enterprise-wide visibility to these dependencies.
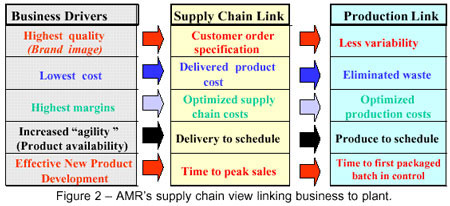
Return to Table of Contents
Case study: Polimeri Europa
Polimeri background
Polimeri installed OSI's SAP-certified PP-PI gateway (RLINK) at six plants in 199five in Italy and one in France. Polimeri is a 50-50 joint venture of EniChem and Union Carbide for the production of polyethylene. The plants used automation systems from several different vendors, including Honeywell, ABB and Bailey. Standard OSI PI (Plant Information) System interfaces were used to collect that DCS data and provide the infrastructure required for a real-time SAP gateway. RLINK provided the connection between the PI system and the central Unix-based R/3 system.
Problems
- Accurate and current information about the process and finished product inventory was not available in SAP for rapid decision making.
- Existing work processes were complex and not integrated across various plant locations.
- Existing procedures required high levels of personal experience, significant duplication of effort and re-entry of data.
- It was difficult to modify existing applications to meet new emerging requirements.
Operation
According to Polimeri, Plant/SAP integration should maximize the efficiency of their plant operations. Each week, SAP downloads a control recipe (generated from a process order) to the plants with each new production campaign, and the recipe has about 75 process instructions (e.g., AMAT, AORD, APROD, APHASE, etc). Engineers have a flexible environment to perform calculations in real-time and analyze current and historical batch data based on SAP order numbers. Each phase completion in the process triggers a partial confirmation to PP-PI with 40 messages containing actual material consumption and the current status of the production campaign.
Results
- Cost data is available in real-time (rather than month-end) to facilitate timely business decisions such as operational efficiency analysis based on production campaign and unit.
- The actual material consumption, material production and equipment utilization that is automatically sent to R/3 can be analyzed when the production campaign is complete.
- There is no duplication of data entry, and the automatic data transfer has eliminated entry errors.
- The accurate inventory provides the basis for ATP (Available-to-Promise) calculations in real-time.
- Process orders were correlated to plant batches and campaigns. SAP understands process orders, but the plant worked in batches and campaigns. The Plant/SAP integration tools provided the cross-reference. This correlation was important because SAP is Polimeri's CIS system for the help desk. Often, they must search through the process order to the actual batch to find quality or process measurements.
- PP-PI electronic batch records provide traceability from raw material to finished product in R/3.
- A key point is that PI-ProcessBook is the one and only interface for plant operators. This eliminates the need to learn SAP screen navigation and reduces the learning curve for plant personnel. These displays are delivered to the users in a web browser.
The display in Figure 3 was created by Polimeri. It shows reactor overviews with details for blenders and silos. It includes order data from R/3 and real-time and historical data from the plant. Once displays are created, they can be accessed by anyone (with security) using a web browser. Any VBA applications included with the display (e.g., programmatically responding to real-time plant events) are also available in the browser.
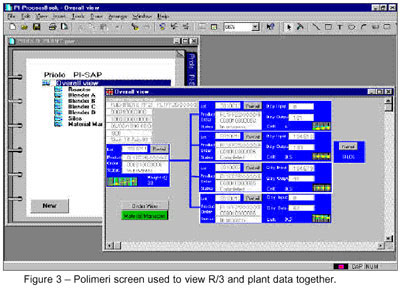
Return to Table of Contents
Case study: Eastman Chemical
Eastman's problem
- 10 different systems
- Seven development tools
- Three database technologies
- Similar in function, diverse in details
- Heavy on support, hard to leverage, aging information technology
- Data duplication and incoherence, lack of analysis tools
Scope
- Implement an enterprise-wide integrated manufacturing information system
- Standardize on "best practices" and drive system requirements through business process improvement efforts
- Deploy a consistent solution to 23 manufacturing sites worldwide, independent of the installed level of process automation technology
Solution
- Eastman standardized on SAP R/3 and they are currently migrating from R/2
- Eastman purchased PI from OSI Software for all their plants
- Eastman purchased the RLINK SAP-certified gateways from OSI to integrate all worldwide manufacturing plants. They installed 2 plants in 1999, and 10 more sites are planned for 2000.
Results
- Eastman has achieved major improvements in its manufacturing operations from the implementation.
- The system automatically gathers, stores, and analyzes data from manufacturing processes. This includes real-time data (e.g., from process control systems), or event data such as the results of laboratory quality tests or operator comments.
- Easy availability of accurate, real-time process data has enabled step change improvements in process trouble-shooting, bottleneck analysis, and process optimization. By transmitting process data to people at all levels, they become problem analyzers and solvers.
- There is no duplication of data entry into R/3, and the automatic data transfer from the manufacturing plants to R/3 has eliminated manual entry errors.
The display in Figure 4 was developed by Eastman, and it is used by operators to:
- Display R/3 orders sent to the plant,
- Select which order to run on which line
- Start and stop batches and automatically report production results to R/3
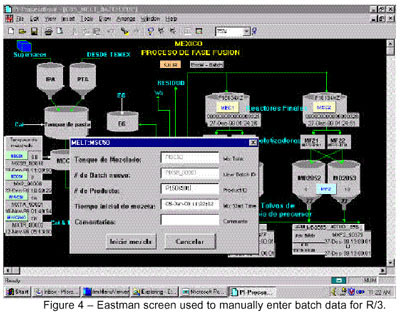
Return to Table of Contents
Conclusion
The Internet and new emerging Microsoft technologies are enabling companies to build tools for the Industrial Desktop to improve the productivity of operators, engineers and managers. The component technologies of today will be the foundation of information technology for years to come. Shrink-wrapped software packages are commercially available to provide access to real-time and historical process and equipment information. Critical information from multiple plants can be integrated with corporate ERP systems. Since each phase of the manufacturing process affects product cost and profit, all employees need to understand how their actions impact the business. Web access to the same information in any format they need is required. Each person can build and maintain their views of the plant for performance monitoring, process and equipment troubleshooting, continuous improvement and innovation.
The results can be summarized as follows:
- Improved efficiency of plant monitoring and diagnosis
- Continuous improvement and innovation
- Improved equipment reliability resulting in reduced unscheduled equipment downtime
- Consistent and comparable information across the enterprise (benchmarking)
- Connectivity to corporate business systems for storing cost data and performing cost-based analysis
The examples shown present process data at the enterprise level via the Intranet. Access to the information is via the Web, enabling personnel located anywhere around the globe to collaborate. The total supply chain is closed, and information is available to improve decision-making.
Return to Table of Contents
REFERENCES
1. Bascur, O.A. and J.P. Kennedy, "Overall Process Effectiveness in Industrial Plants", Latin American Mining Perspectives Proceedings, O.A. Bascur, Ed, SME, Littleton, CO, USA, 1998, 293-306.
2. Bascur, O.A. and J. P. Kennedy, "Industrial Desktop - information technologies in metallurgical plants," Mining Engineering, 1996, September.
3. Bascur, O. A., 1991, Human Factors and Aspects in Process Control Use, Plant Operators Symposium, SME, Colorado, pp.85-94.
4. Bascur, O.A., and Kennedy, J.P., 2000, "Mineral Processing Process Optimization and Collaboration at the Industrial Dektop," XXI International Mineral Processing Congress, July.
5. Bascur, O.A., and Kennedy, J.P., 2000, ‘Web Enabled Industrial Desktop, Enterprise Process Collaboration", IFAC Conference, Helsinki, August
Return to Table of Contents