The Impact of Methyl Ethyl Ketoxime
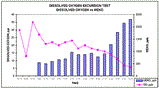
By Douglas B. DeWitt-Dick and Kaj D. Rondum, Ashland Specialty Chemical Company, Drew Industrial Division
Abstract
Corrosion and flow assisted corrosion (FAC) of condensers, feedwater heaters, feedwater piping and economizers result in forced outages, which cost the utility industry millions of dollars in maintenance. In many instances, they require the purchase or generation of power at elevated cost.
The accumulation of the products of corrosion in the generating tubes of steam generators also contributes to corrosion, and eventually these deposits must be removed through chemical cleaning.
Methyl ethyl ketoxime (MEKO) was first successfully introduced to the utility industry more than 10 years ago as a replacement for hydrazine. Initial work entailed monitoring dissolved oxygen in both the condensate pump discharge and deaerator outlet. At low ppb levels of MEKO, the dissolved oxygen levels in both streams were maintained or reduced. Users also noted a dramatic reduction in the quantities of metal oxides removed during the normal five-year operating cycle.
Subsequent applications at several stations demonstrated MEKO's ability to control dissolved oxygen, even under upset conditions. Also, the levels of iron and copper oxide corrosion products generated in the feedwater circuit reduced significantly.
This has been attributed to the change in oxide film morphology in the presence of MEKO. The oxide film generated tends toward g-iron oxide, which is more resistant to FAC than the magnetite film formed under the hydrazine regime.
Recently, rigorous testing also demonstrated that deposit weights can be reduced in the generating tubes of these high-pressure utility steam generators during normal operation. This allows the plant to extend the period of time between chemical cleaning and reduces the potential for corrosion of the boiler tubes because of metal oxide deposition and subsequent chemical cleaning.
This paper presents data on the impact of MEKO on dissolved oxygen control, reduction in the generation and transport of metal oxides in the condenser/feedwater circuits and deposit reduction in the steam generators. Also, the effects of MEKO on cation conductivity, organic acid generation and condensate polisher resin will also be addressed. Through the proper application of this oxygen scavenger/metal passivator, corrosion throughout the entire utility steam cycle can be reduced.
Introduction
Presently there are more than 65 units in central utility power stations using MEKO as their primary oxygen scavenger/metal passivator. The data contained in this paper came from extensive evaluation at many of these stations. The field evaluations were designed to further document and support ongoing laboratory and research projects in the areas of metal oxide film formation and metal passivation.
Dissolved Oxygen Reduction
The initial MEKO application in a 2600 psig (177 bar) utility circuit occurred in 1988 to demonstrate that dissolved oxygen could be suppressed to the same extent as hydrazine. Subsequent evaluations in other units confirmed the data generated in the initial study.
In one trial at a 2800 psig (190 bar) utility, MEKO performed significantly better than other oxygen scavengers for dissolved oxygen removal particularly in the condensate pump discharge sample point. MEKO was able to consistently reduce dissolved oxygen levels to the range of 0.5-2.0 ppb.
In another study, an oxygen excursion test was undertaken to simulate a mechanical malfunction of the deaerator, which would subsequently result in elevated feedwater dissolved oxygen levels. The purpose of the test was to determine the effectiveness of MEKO in returning the system's out-of-specification feedwater dissolved oxygen to within the predetermined control limit (<10 ppb).
From the time the MEKO feed was reinstituted, the dissolved oxygen concentration started steadily decreasing from about 35 ppb down to 5 ppb, during which time the corresponding MEKO concentration in the system rose.
Overall, the dissolved oxygen level trended downwards while the corresponding MEKO concentration trended upwards. The evaluation was completed after determining that MEKO was able to reduce the elevated level of dissolved oxygen to levels below 10 ppb and was able to maintain those levels for 60 minutes. The data from this study is shown in Figure 1.
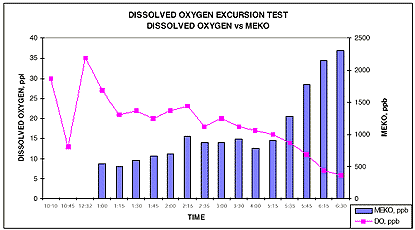
Numerous additional utility applications of MEKO show consistent feedwater dissolved oxygen reduction to a range of 0.5-2.0 ppb with corresponding oxygen scavenger control ranges of 25-75 ppb.
Iron and Copper Reduction
During monitoring of the system chemistry at the initial evaluation site, it was noted that the feedwater iron and copper concentrations also decreased under the MEKO regime (Figures 2 and 3).
This work was followed by further studies at several other stations with similar results. It was noted that the films formed under the MEKO treatment were maroon in appearance rather than the traditional black magnetite. Using FTIR analysis, the film was identified as a g-iron oxide (Fe2 O3) species known as maghemite.
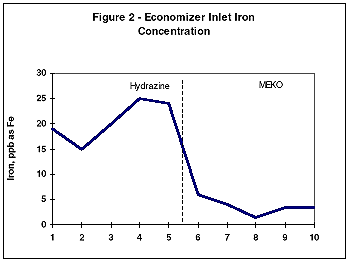
This film is very similar to the film formed under oxygenated treatment, and appears to be far less susceptible to flow assisted corrosion than the magnetite films formed under hydrazine or other similar treatments.
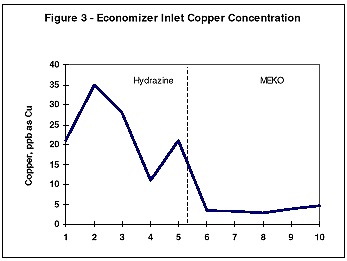
As the potentiodynamic corrosion resistance of both the g-Fe2 O3 film and the Fe3 O4 film are similar, the reduction in iron oxide through the feedwater cycle under the MEKO regime can, at least in part, be attributed to the resistance to flow assisted corrosion. This is graphically depicted in Figure 4.
While most utility feedwater heat exchangers have stainless steel or copper/nickel tubes to reduce waterside corrosion potential, iron transport can result from improper corrosion inhibition of the carbon steel metallurgy of the shell. Since most of these systems return extraction condensate to the boiler feedwater circuit, these iron oxide particulates can aggravate or promote a flow-assisted corrosion phenomenon typically manifested in the economizer section.
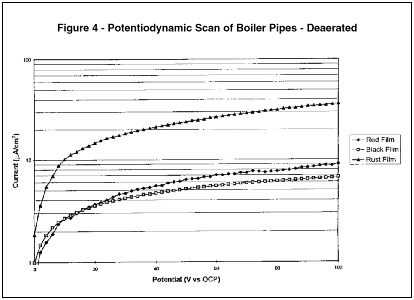
MEKO survives elevated temperatures exceeding 1000ºF (538ºC) as evidenced by measurable quantities of the product in the turbine crossover steam, indicative of its excellent thermal stability and survivability.
This unique capability ensures protection of the feedwater heat exchanger shell side, thereby minimizing subsequent transport of metal oxides to the feedwater circuit. Its superior oxygen scavenging and metal passivating characteristics reduce and maintain feedwater iron levels in many systems to 1 ppb or below.
The reduction in metal oxide pickup through the feedwater circuit was further verified when the unit initially treated with hydrazine switched to MEKO. During the previous major outage, the unit was chemically cleaned and 4,100 pounds of iron and 17 pounds of copper were removed. After the MEKO treatment, the unit was chemically cleaned using the same cleaning procedure as before and 500 pounds of iron and 10 pounds of copper were removed.
This corresponds to an 88% and 41% reduction in iron and copper, understanding that during the first two years, the unit was still on hydrazine. To reduce the costs associated with chemical cleaning, plant personnel decided to use deposit weight analyses as a means of determining when to clean the unit. The results of these analyses for this plant are listed in Table 1.
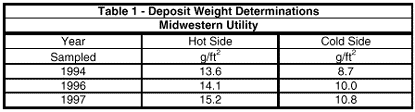
Cleanup
Work at another utility station that used deposit weight analysis for many years to determine chemical cleaning requirements verified that MEKO does maintain clean internal boiler tube surfaces.
Deposit weight density data from this station comparing hydrazine and MEKO is shown in Table 2.
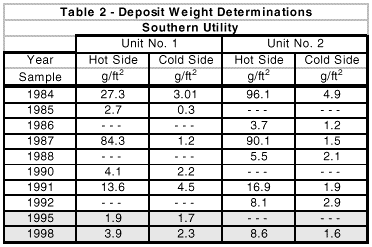
(Note: Units 1 and 2 were chemically cleaned in 1984, 1988 and 1991. Results of MEKO usage are indicated by the shaded areas.)
Additional comparisons of corrosion mitigation throughout the circuit are shown in Figures 5 through 8. Iron and copper corrosion product concentrations show significant reduction when the operating units were switched from hydrazine to MEKO.
Based upon independent consultant DWD analyses and recommendations, neither unit has required chemical cleaning since switching to MEKO in 1992 and 1993.
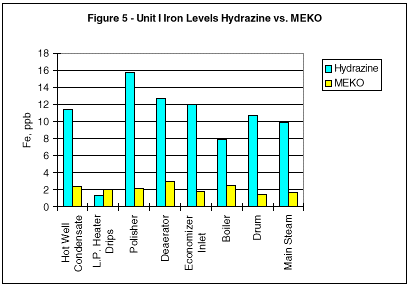
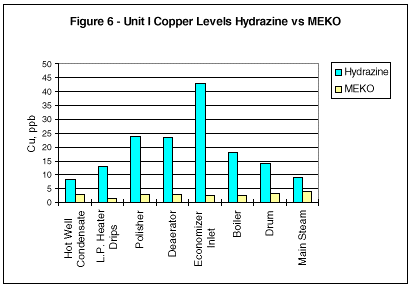
A utility station in the Southwest operating in the cycling mode experienced very high deposit weights in its unit (see Table 3). The station has a 165 MW steam turbine-generator set driven by 1005°F (540°C) superheated steam from an 1870 psig (127 bar) Babcock & Wilcox boiler.
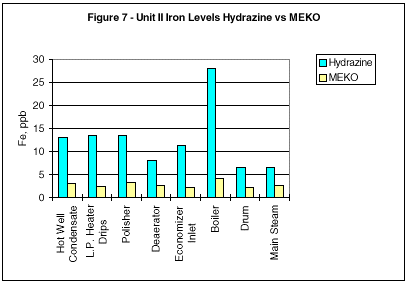
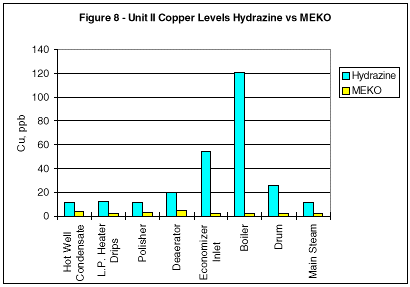
Money was not budgeted for chemical cleaning; consequently, the decision was made to put the unit back into service and chemically clean during the next annual outage. To maintain the unit at the existing levels of deposit density, plant personnel selected MEKO. It was recommended that they operate the unit at elevated MEKO levels to maintain cleanliness.
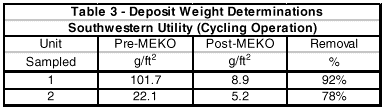
During the first two weeks of treatment, they experienced "crud bursts" from the boiler as indicated by black water. In conjunction with the elevated levels of metal oxides in the blowdown, the internal boiler water chemistry was upset in that pH dropped and phosphate residuals rose.
This condition indicated that the unit was cleaning up. After about two weeks, the blowdown cleared up and the internal boiler water chemistry lined out. During the subsequent annual outage, the chemical cleaning company was prepared to clean the unit. Tube sections were removed for deposit weight analysis. Based upon the results shown in Table 3, the plant cancelled the chemical cleaning. This netted an avoided cost of more than US$100,000.
A boiler plant operating at 1500 psig (102 bar), 975°F (524°C) superheated steam experienced failures in the nose arch tubes. The failures resulted from long-term overheating from oxide deposition in the sloped tubes just below the bends. Based on the results obtained at the Southwestern utility station, it was recommended that MEKO feed be established at 300 ppm to 500 ppm in the boiler.
As can be seen in Figure 9, when the MEKO residual in the boiler was maintained in the recommended range, iron and copper transport rose to greater than 100%, indicating some cleaning activity. The percent transport continued to rise for a period of two months before it started to decline.
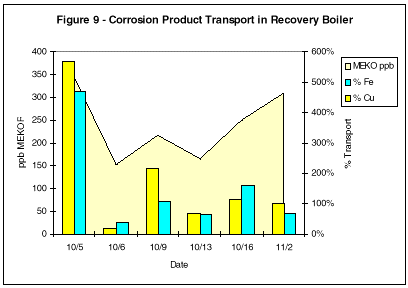
At this point, the unit was considered clean. No further failures have been experienced in the five months that the plant has used this treatment program.
Organic Acids and Cation Conductivity
The presence of organics in a system comes from various sources including, but not limited to, raw makeup water, lubricants, ion exchange resin sloughage and treatment chemicals. These compounds can undergo hydrothermal degradation to form organic acids, which can result in an increase in the cation conductivity.
Other factors such as demineralizer and polisher upsets and/or slippage, load changes, condenser leakage and start ups following outages can cause increases in cation conductivity as well.
MEKO is an organic molecule and consequently, there were concerns about potential breakdown products, in particular organic acids and their impact on cation conductivity. A number of operating stations using MEKO were sampled at various points including the condensate pump discharge, economizer inlet and main steam.
These samples were tested using high purity organic acid analysis by capillary electrophoresis. The results, for the most part, showed levels below 5 ppb for propionic acid and less than 3 ppb for formic and acetic acid. Also, cation conductivity at numerous generating stations was monitored. As expected, it varied considerably from low levels of 0.1-0.2 mmhos/cm to intermediate values of 0.5-0.6 mmhos/cm up to upper levels of 1.2 mmhos/cm.
None of the utilities have experienced any negative effect associated with the use of MEKO.
Polisher Resins
A utility station in the Midwest has been operating under MEKO treatment for eleven years, employing full flow mixed bed condensate polishers. To date, it hasn't seen any deleterious effects on polisher performance.
MEKO passes through the polisher, allowing it to protect the low-pressure feedwater cycle. A station in the Southwest has been using MEKO for the past nine years and hasn't seen any degradation in performance of its full flow mixed bed condensate polishers. This is important because MEKO is volatile and survives superheat and reheat. Consequently, it is found in the condensate pump discharge.
Summary
For more than a decade, MEKO has proven effective in suppressing dissolved oxygen throughout the utility steam cycle. The protective film formed appears to be less susceptible to flow assisted corrosion than the magnetite film formed with most of the other scavengers. This results in reduced metal oxide transport into the boiler and reduced metal oxide deposition in the boiler.
At elevated dosages, MEKO contributes to removal of oxides from the boiler. This can extend the time between chemical cleaning, reducing overall costs and extending boiler life expectancy. The use of MEKO does not adversely effect the cycle chemistry or the performance of ion exchange type condensate polishers.
For more information about MEKO and the data contained in this technical paper, contact Anne Cantafio, arcantafio@ashland.com, 973-263-7745.
Edited by April C. Murelio
editor@poweronline.com