The Future of Level Detection Technology Pt. III

By Christoph Rompf, Product Manager for Level Measurement, Endress Hauser GmbH Co. and Jerry Spindler, Business Development Manager, Endress Hauser Instruments.
Advanced technology today
This may all seem too futuristic or far advanced to be practical for just a liquid level switch. But, it is in fact readily available today.
Endress Hauser Instruments, Inc. invented and patented the first level detection devices incorporating the tuning fork concept in 1966. The first product was a level detection instrument for solids, which was followed shortly thereafter with a level detection instrument for liquids, called the Liquiphant. Recognized as the pioneering leader in tuning fork technology, E H continues to introduce new innovations in this area while maintaining their commitment to continued future advancements.
The third generation tuning fork product from E H incorporates further advances in tuning fork development. Liquiphant M was introduced in the US in January 2000. E H maintains worldwide leadership in tuning fork technology, which is demonstrated by the superior performance of this product. After installing more than one million Liquiphants worldwide and accumulating three decades of field experience, E H has gained the practical knowledge no one else can match to be world leader in this technology.
To facilitate verification, testing, and optimization of application safety (even during the development phase), Endress Hauser invested heavily in an independent department for the simulation of complex processes in sensor and application technology more than 10 years ago. This department uses computer-aided methods, e.g. the finite element method, to simulate material stability and product behavior (see Figure 8). The finite element method modeled the mechanical structures of the Liquiphant sensor with small elements and determined deformation, tension, compression, and oscillation under stress conditions via elasticity-specific interdependencies. Apart from determining these theoretical interdependencies, application-oriented solutions in piezo technology were also investigated under laboratory conditions in this Advanced Application Technology Department.
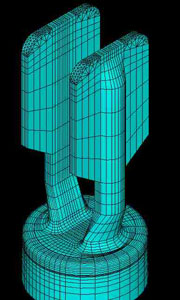
The tuning fork of the Liquiphant M operates at its resonant frequency by a piezoelectric drive via the sensor's diaphragm. Depending on the mass moment of inertia of the fork, the frequency is approximately 1000Hz in air. Such a high frequency eliminates the risk of the sensor being effected by surrounding facility vibrations, e.g. those of connected motors.
The patented "bi-morph" piezo system is a recent innovation in which a piezo disk is permanently bonded to a ceramic disk, creating the deflection to drive the vibration (Figure 8). This approach, with two (BI) materials combined (MORPHED) together, further improves reliability and allows installation into even smaller, confined spaces since the tuning fork is now a mere 1.5 inches in length.
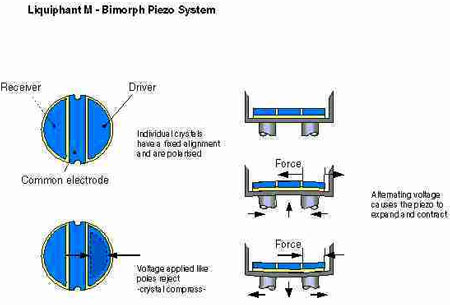
Industry-specific housings for the chemical, pharmaceutical, and food and beverage industry, along with the appropriate selection of process connections (including sanitary) and approval certificates, ensure optimum adaptation to a wide range of diverse applications. An assortment of electronic inserts (Figure 10) offers a suitable output signal to any PLC, process control systems, or fieldbus systems. NEMA 4X housing ratings protect the electronics, plus the inserts are potted inside a molded body that just plugs into the sensor. A breather element is added to the housing to eliminate any internal condensation.
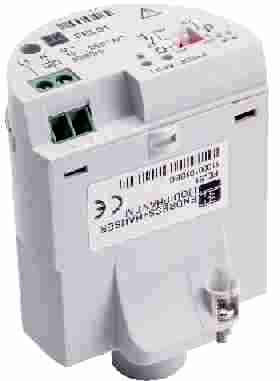
Detection of levels in liquids forms part of standard process control techniques in all industries, ranging from the chemical industry to the sanitary areas of the pharmaceutical and food industry. The ideal level detection instrument can be employed in all applications and offers – despite its versatility – maximum dependability and safety in any specific application. In recent years, the Liquiphant sensor's tuning fork principle, with its simplicity, high degree of dependability, and universal application range with the welcomed absence of maintenance requirements, has emerged as the preferred method in all industries worldwide.
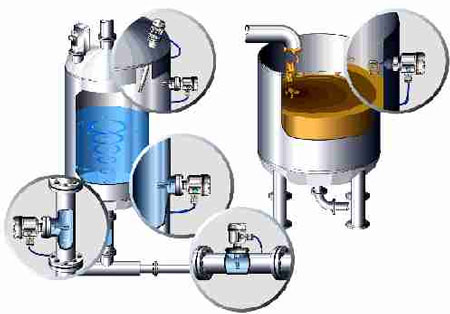
Multiple methods of installation exist, including top mounting for monitoring maximum level, bottom mounting for monitoring minimum level, side mounting for high/low level, or pipe mounting for pump protection.
The range of applications for the Liquiphant M include:
- Limit detection in any liquid that can still be pumped
- Process tanks, emulsion tanks, pipes (where the small size of the sensor is critical), storage tanks
- Liquids with a proportion of solids, or aggressive media
- Medium with a density from 0.5 SGU and up
- Process temperatures of –40°F to 300°F
- Pressure range of 0 to 600 psi
- Viscosity up to 10,000 cP
Turbulence, vibration, solid content, sticky media, bubbling or foaming liquids, build-up, or abrasion by aggressive media will not affect performance.
Conclusion
One might think that the "advanced" technology of a tuning fork device carries a hefty price when initially purchased. Amazingly, however, it is in the same price range as alternate technologies (such as ultrasonic gap or capacitance systems) or even less, while it comes with all of the added benefits mentioned above. Today, as many multinational companies have processing facilities scattered all over the globe, the ability to economize and standardize on instrumentation means that a supplier must have a presence around the world. E H serves the entire planet with production facilities strategically located in 19 countries, and a vast network of sales and service centers locally operating in more than 60 industrialized nations. With this level of support, and the products designed for the tough demands of future industrial applications, the new Liquiphant M is the right choice for all liquid level detection needs, no matter where they might be located. Positioned as the largest independent instrumentation company in the world, and the #1 supplier of level measurement instrumentation, E H can offer the most advanced solutions for nearly any process level application, including Radar (microwave), Ultrasonic, Differential Pressure, Hydrostatic, Microimpulse Time-of-Flight, Capacitance, Reverberation, and Vibration.
For more information: Endress Hauser, Inc., PO Box 246, 2350 Endress Pl., Greenwood, IN 46142. Phone: 800-428-4344 or 317-353-7138. Fax: 317-535-8498.
To purchase Liquiphant M and other Endress Hauser measurement products, click here.
Subscribe to our free e-mail newsletter.
Click for a free Buyer's Guide listing.