The Cansolv System Process: A New Paradigm for SO2 Recovery and Recycle (Part III)
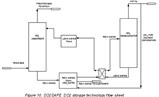
Cansolv Technologies Inc.
8475, avenue Christophe-Colomb, Suite 2000
Montreal, Quebec, H2M 2N9 Canada
http://www.cansolv.com
The Cansolv System is an aqueous amine-based regenerative gas desulfurization process that promises SO2 removal down to a few ppm. The first section of this paper looks at process technology. The second section explores potential uses in a broad range of applications. The final installment describes the application of the technology to SO2 transportation and storage, as well as pilot tests using the technology.
Contents
Cansolv system technology
Pilot testing
Gas stream conditions
Test results
Conclusions
Safe SO2 Storage and Transport
Sulfur dioxide, SO2, is a widely used chemical in industries such as wood pulping and bleaching, corn wet milling, water treatment and the production of sulfuric acid. It is a colorless, non-inflammable toxic gas, with a boiling point of -10.0`176C at atmospheric pressure of 1013 mbar. Currently, the normal method of storing and transporting bulk quantities of SO2 is as a liquefied gas in suitable pressure vessels. This presents a serious risk due to the possibility of a catastrophic release of SO2 in the case of storage vessel or fitting failure. In such a case, while the probability of occurrence is low, the effects are extremely serious. Gaseous SO2 is very toxic, showing adverse health effects at concentrations as low as 3 parts per million. Since SO2 gas is heavier than air, any release will tend to stay at ground level, maximizing human exposure.
The majority of SO2 for captive use or for merchant sale is produced either by sulfur burning or by capture from metallurgical gas streams. Both processes are rather expensive and the latter usually requires transportation over long distances to the consuming site. Since transportation routes often pass through metropolitan centers, large segments of the population are exposed to risk in case of a spill. On the other hand, SO2 produced by burning sulfur-containing fuel is either emitted as a pollutant or turned into low-value gypsum by limestone scrubbing. The Cansolv SO2 scrubbing technology, when combined with the SO2SAFE SO2 Storage and Transportation process, addresses both issues by enabling economical, safe and efficient pollution control and SO2 recovery and recycle.
Cansolv system technology
The Cansolv SO2 scrubbing process utilizes an aqueous amine absorbent that is highly selective for removal of SO2 from various gas streams such as flue gas. The process flowsheet is very similar to the well-known alkanolamine process for removal of H2S and CO2 from natural gas and refinery gas streams. The essence of the process is absorption of SO2 into the solvent in an absorber and recovery by stream stripping in a regenerator. The byproduct SO2 is recovered as a pure, water saturated stream and the regenerated solvent is recycled to the absorber. Removal of SO2 from the feed gas to <10 ppmv is economically viable.
A patent application has been filed for the SO2SAFE SO2 storage technology, which is an extension of the Cansolv scrubbing process. It consists of storing and shipping the SO2 dissolved in the absorbent and regenerating the absorbent at the user's site on demand. The same or a different absorbent may be used for scrubbing and storage, depending on the specific requirements of a particular application. A 25-30% solution of the amine in water is utilized in the process. These absorbents provide significant advantages:
- since the amine absorbent is always present in the process as a salt, it is totally non-volatile and equilibrium vapor phase losses of solvent to the treated gas are zero
- the product SO2 is pure with no amine contamination
- a high usable loading of SO2 in the rich solvent
- up to about 1 equivalent of strong acid anions per mole of amine, i.e. heat stable amine salts (HSAS), may be present in the absorbent without decreasing the normal scrubbing capacity by the sorbing nitrogen
- HSAS are removed easily and efficiently by a patented electrodialysis process
- inhibition of SO2 oxidation to sulfate by oxygen
- high thermal and chemical stability
For economy in transportation cost, the rich amine produced by scrubbing a feed such as flue gas may be further loaded with SO2 by saturating it to an SO2 vapor pressure of close to one atmosphere with the pure SO2 produced by regenerating a part of the rich amine from the scrubber. In this manner, transport of SO2 in SO2SAFE Solvent within a radius of some 500 km is economically competitive. A simplified process flow diagram for the production of rich SO2SAFE Solvent is shown in Figure 10.
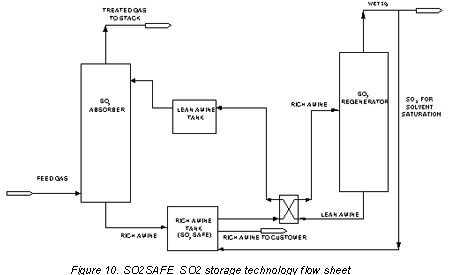
Loss of containment. The vapor pressure of liquid SO2 at temperatures that may occur in normal storage and transport operations can be up to 8 bar. Thus, in case of a leak in or rupture of the pressure vessel used to store or transport liquid SO2, particularly if the damage occurs towards the bottom of the vessel, large quantities of SO2 can be released from the tank very rapidly. Since the SO2 at ambient temperature is above its boiling point, any liquid SO2 released to atmosphere will vaporize rapidly, creating a vapor cloud of toxic gas that tends to stay at ground level, being heavier than air. Prevailing winds can then disperse the vapors, creating conditions hazardous to health or even lethal conditions over a large area. Concentrations of 5–10 ppmv of SO2 in air will lead to irritation of the respiratory tract and concentrations above 400-500 ppmv, even for a few minutes, are dangerous to life. Areas adjacent to industrial SO2 storage sites and railroads or roads used for the transport of SO2 are thus at risk in the event of such a release.
The release of SO2 from solution in the SO2SAFE SO2 solvent is much less and slower. While the initial partial pressure of SO2 over the solvent is up to 1 atmosphere, evolution of the gas from solution is inhibited by a) formation of a liquid side SO2 depleted boundary layer which decreases the mass transfer rate, and b) cooling of the liquid by the heat of vaporization of the SO2 which i) decreases the equilibrium vapor pressure and ii) increases liquid viscosity, making the boundary layer thicker.
The impacts from the loss of containment of a storage tank containing SO2 rich solvent and liquid SO2 are compared in Table 1. An average SO2 partial pressure of 0.0188°bar absolute over the rich SO2SAFE solvent was assumed for dispersion modeling. The impacts from the loss of containment of storage tanks containing SO2 rich solvent and liquid SO2 are compared in Table 1.
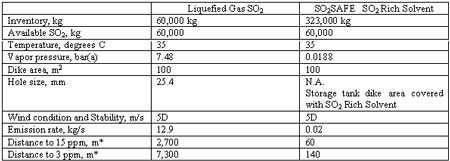
*Dispersion calculations done with Phast Version 5.01 software
The distances to similar toxic concentrations of SO2 are much shorter for a loss of containment of SO2 rich solvent than for liquefied gas SO2 : 60 m vs. 2,700 m for 15°ppm and 140 m vs. 7,300 m for 3 ppm, respectively. The loss of containment consequences for the SO2 rich solvent are thus almost three orders of magnitude less than for liquid SO2. In an urban SO2 storage facility, liquid SO2 storage has the potential to affect a large population, while the SO2 rich solvent impacts only the immediate vicinity of the site. The SO2SAFE SO2 rich solvent is by its nature intrinsically safer.
Pilot testing
Flue gas. The generic Cansolv scrubbing process was successfully piloted during a 9-month trial in 1991 at the Suncor Oil Sands plant in Fort McMurray, Alberta, in flue gas desulfurization service. Removal rates in excess of 99% were consistently demonstrated. The absorbent was found to be very stable and capable of effecting high removal rates at low liquid to gas ratios. The unit operated from February 28 to November 28, 1991, scrubbing 3600 scfm of flue gas from the site's utility boilers. The fuel in the boilers was petroleum coke produced in the tar upgrading process and had a sulfur content of 7%. On many occasions in the course of performing the statistically designed experiments, SO2 in the treated gas was <15 ppmv. Results of the test program exceeded expectations and demonstrated the Cansolv System process to be robust, effective and easy to operate.
Metallurgical gas/pulp & paper. CTI designed and constructed a highly versatile mobile pilot unit, for the purpose of demonstrating Cansolv technology and obtaining fundamental site-specific scaleup data. The pilot plant unit is mounted on a 16-foot trailer. It consists of a 13 foot, 4-in. ID insulated absorption tower with structured packing mass transfer elements and an 18 foot, 4-in. ID insulated regeneration tower, also containing structured packing. The regenerator has a steam heated reboiler, and an overhead condenser and condensate accumulator. The associated peripheral equipment consist of three process pumps, a plate and frame heat exchanger, a vacuum pump, a feed gas blower, two absorbent particulate filters and an activated carbon filter. The Cansolv System mobile pilot plant also includes an absorbent heat-stable salt removal unit based on the principle of electrodialysis.
Feed gas containing SO2 enters the absorption tower, where the Cansolv Absorbent DS solvent picks up the sulfur dioxide, thus cleaning the effluent gas down to a few ppm SO2. The solvent is then regenerated in the regeneration tower and returned to the absorption tower in a cyclical mode to pick up additional SO2. Instrumentation for monitoring process parameters consists of local indicators. Gas SO2 concentration is monitored with a non-dispersive infrared process analyzer.
The unit was commissioned and run in at a metallurgical acid plant. Both acid plant feed and tail gases, at 7.5% and 1500 – 2000 ppm SO2 respectively, were treated. The treated gas in both cases had less than 50 ppm SO2 and the unit performed satisfactorily in all respects. It was then moved to the pulp mill for the trials.
The results obtained with this small-scale pilot unit were consistent with data available from previous large scale (6,000 Nm3/h gas flow) testing and from a rigorous thermodynamic process model on the Aspen Plus platform .
Gas stream conditions
Field tests were run at an ammonia based sulfite mill on both blowpit gas and recovery boiler flue gas. The two streams are quite different, as can be seen from Table 1.
TABLE 1
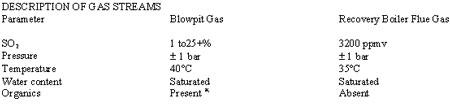
* The organic content was not quantified. Compounds identified by GC/MS included methanol, acetone, furfural and p-cymene .
The blowpit gas presented the greater challenge due to the highly cyclical SO2 concentration resulting from the batch nature of the digester operation. When a cook was blown into the blowpit, a large fraction of the unreacted free SO2 flashed off with the steam generated from the superheated cooking liquor. This gas stream also contained organics originating from the wood resin and from the reaction products of the cooking process. Prior to being treated for SO2 removal, the blowpit gas is cooled in direct and indirect coolers. Between blows, a vacuum relief valve admits air into the blowpit.
The recovery boiler flue gas results from the excess air combustion of SSL concentrated to a solids level of about 55-60% and therefore has a high water content. Prior to SO2 removal, it is cooled and saturated in a direct cooler.
Test results
Very high removal of SO2 was obtained from both gases. The treated recovery boiler flue gas had SO2 concentrations consistently below 30 ppmv at steady state operation. Due to the cyclicality of SO2 concentration in the blow pit gas, the absorbent flow rate was increased for the duration of the SO2 peak during a digester blow. This minimized the average absorbent flow rate. Treated blowpit gas contained less than 45 ppm SO2, proving the load following capability of the Cansolv System process.
The water saturated SO2 byproduct from blowpit gas contained only very minor quantities of organics, demonstrating the capability of the process to reject these and prevent their accumulation in the overall mill process. The SO2 produced was greater than about 95% purity, with the balance being essentially water. In particular, no Cansolv Absorbent DS could be detected in the byproduct SO2.
The total on-stream time of the test was about 160 hours. No adverse effects on the absorbent or treating performance were noted.
Conclusions
The Cansolv System Process has introduced a new paradigm for SO2 recovery and recycle, by simultaneously reducing toxic emissions and cost.
The field testing of the Cansolv scrubbing process demonstrated the ability to recover and recycle SO2 from metallurgical gas and in a sulfite pulp mill, as free SO2. Extremely low levels of SO2 emissions are achievable, while reducing plant complexity and costs. The decoupling of recovery and pulping operations will reduce operating complexity and constraints.
The excellent results obtained on the four different gas streams tested with the unit support the general applicability of the technology to other uses such as in smelters, acid plants, flue gas desulfurization, refineries and sulfur recovery units. A larger test unit is under construction for demonstration of the process.
Edited by Alan S. Brown
Managing Editor, Chemical Online