ROSS V Cone Blenders Ideal For Gentle And Effective Mixing
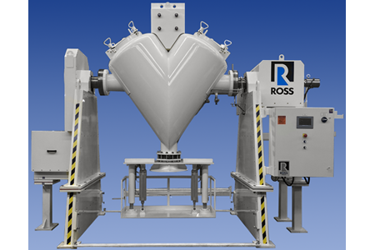
Hauppauge, NY — Offering a high level of precision and consistency, ROSS V Cone Blenders utilize diffusion as the main mechanism for mixing. As the V shaped vessel rotates on its horizontal axis, batch materials cascade down, distributing particles over a freshly exposed surface. With operating speeds of 5 to 25 revolutions per minute, the ROSS line of tumble blenders can easily mix dry solid blends (including high density powders), low-viscosity slurries, friable materials, as well as formulations containing trace components and/or ingredients that are dissimilar in size, shape and density.
The purpose-built ROSS Model VCB-20, pictured below, is fully customized with two (2) pneumatic cylinders affixed to the V cone body to disconnect and connect fiber drums for charging and discharging. The blender’s dust-tight butterfly valve is operated by optional pneumatic control. To reduce the size of agglomerates, a high-speed intensifier bar is installed along the mixer’s axis of rotation. Nozzles can also be attached to this intensifier bar for continuous liquid additions during the mixing process.
Carbon steel legs provide a 40” clearance beneath the discharge valve to the floor, as well as safety guardrails that are strategically positioned at the front and rear of the mixer. The front railing consists of two sections, each equipped with safety switch interlocks. The rear railing is stationary to prevent access to the rotating area of the mixer, ensuring operational safety.
The NEMA 12 Control Panel includes a 7” touchscreen for viewing and controlling the blender’s and intensifier bar’s rotational speeds. The controls package also includes a jog function, emergency stop pushbutton, motor fuse protection, rotary disconnect, as well as proximity switches to stop the blender at certain preferred positions, and relay logic control for precise operation of the drum lift mechanism.
Source: Charles Ross and Son Company