Powdex '99: Kason Introduces New Inline Separator, Fluid Bed Dryers
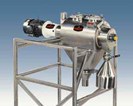
Centrifugal Separator
Kason's new Centrisifter inline centrifugal separator replaces cyclone separator-rotary air lock combinations in dilute-phase pneumatic conveying systems. Rated for use between 14.9 psig down to 14 in. vacuum, the unit separates virtually all free-flowing conveyor- transported materials at equivalent capacities.
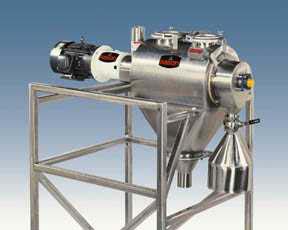
The heart of the unit consists of rotating helical paddles within a cylindrical screening chamber. The paddles, which never touch the screen, continuously break up and accelerate incoming particles through screen apertures.
Oversize material accumulates immediately upstream of a manual or automatic valve, which ejects trash into a sealed, quick-release receptacle. The sealed separators have large inspection doors for two- minute screen changes and wash down of all smooth interior surfaces.
Kason can build the units to 3A, USDA, FDA, BISSC and other sanitary standards. The company also provides a broad range of screens, including woven nylon, monofilament, and stainless steel screens, as well as stainless steel wedgewire.
Potential uses include sifting, scalping, dedusting, dewatering, and delumping. The company provides a broad range of sizes and configurations, including low-profile models, twin configurations, and gravity-fed units.
Fluid Bed Dryers
Kason also introduced two new circular fluid bed dryers. The 40-in. dia and 48-in. dia models fill in its range of eight units ranging in diameter from 18 in. to 84 in.
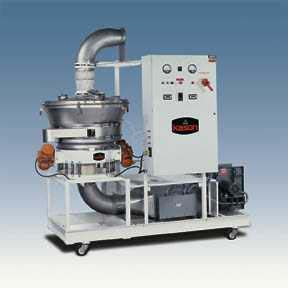
The company says the 40 in. unit is more efficient and easier to clean than traditional rectangular fluid bed processors. One reason is the circular design's inherent rigidity, which lets Kason downgauge materials of construction, downsize vibratory motors, and weld fewer seams. Unlike rectangular units, the circular design requires only one air inlet and outlet. As a result, it costs less to fabricate, especially when finished to FDA, USDA, BISSC or 3A standards.
The resulting unit is lighter, smaller, and more efficient than rectangular units of equivalent capacity, says Kason VP Henry Alamzad. This allows Kason to configure complete systems (including blower, heater and controller) on caster-mounted frames. They roll into place and plug directly into a power source, dust collector, and material inlet/outlet.
With fewer weld seams, a quick-disconnect housing, and no internal cross members, it takes about half as much time to clean the fluid bed dryer, the company says.
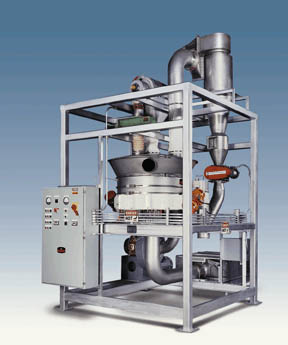
The company's 48-in. dia system is part of a ready-to-run, skid-mounted fluid bed dryer system. In addition to the 48-in. dia circular fluid bed processor, it includes a heater, blower, cyclone separator, and optional Centrisifter centrifugal separator (above the fluid bed unit) for continuous de-lumping of incoming material.
Like all Kason unit, the fluidized bed dryers are configurable for drying/heating, cooling, or moisturizing. Kason also manufactures circular vibratory screeners and specialized separation equipment for sifting, scalping, classifying, dedusting, delumping and dewatering, as well as agglomerating and powder coating.
Details: Henry Alamzad, VP, Sales and Marketing, Kason Corp., 67- 71 East Willow St., Millburn, NJ 07041-1416. Phone: 973-467-8140. Fax 973-258-9533.
By Alan S. Brown