Hydroxylamine Shortage Spurs New Capacity, Alternative Technologies
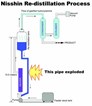
BASF AG (Ludwigshafen, Germany) will boost capacity for hydroxylamine free base (HAFB) 50% solution at its Ludwigshafen plant to 4000 mt/yr by the end of September 2000.
In addition to stretching capacity through ongoing process improvements, BASF may build a second plant in the United States to meet growing demand. It expects to make a decision on the investment within the next few weeks.
BASF first developed its HAFB process in February, 1999, and only began producing electronics grade chemical this year.
Shortages Loom
The decision to boost capacity comes after a June 10 explosion that shut down the world's only other hydroxylamine plant, the Nisshin Chemical unit in Ojima, Japan. An explosion destroyed a third hydroxylamine plant owned by Concept Sciences Inc. (Lehigh Valley, Pennsylvania) 16 months earlier.
Though reports from Nisshin are still incomplete, it is not clear when, or if, the facility will resume production. Repairs are likely to take 2-3 months, and a planned second production system is reported to be 2-3 months from completion. However, the plant is located in a residential area and may face local opposition in the wake of the explosion.
HAFB is widely used by the semiconductor industry to remove photoresist and etch residues during the fabrication of integrated circuits. A recent survey found 80% of International Sematech (Austin, Texas, USA) were using HAFB cleaning chemistries. It is also used to synthesize pharmaceuticals and to treat metal surfaces.
Worldwide hydroxylamine shortages appear imminent. "We are doing everything to meet the world demand for HAFB as soon as possible," says BASF head of the inorganics marketing Hans Bartels. "Short term certain allocations will be unavoidable. Our customers have been informed, and we are working out supply programs with them."
Explosive Situation
Hydroxylamine is sensitive to heat and prone to explosion. Producers typically ship it as a solution containing stabilizers. Even so, the Nisshin Chemical unit was not the first to suffer from an explosion.
Concept Sciences made the chemical using a proprietary process that combined hydroxylamine sulfate and potassium hydroxide. This yielded a 30% hydroxylamine solution and potassium sulfate. After filtering out the potassium sulfate, it distilled the hydroxylamine at 120 F to remove any water and solids. An explosion, likely caused during distillation, destroyed the Concept Sciences plant and killed five on February 19, 1999.
The Nisshin explosion appears to have occurred in the final concentrator. Early Associated Press reports put the human cost of that explosion at four dead and 27 injured.
The dominant US formulators of HAFB strippers and products are Ashland-ACT, part of Ashland Specialty Chemical Co. (Dublin, OH), and EKC Technology, Inc., a subsidiary of ChemFirst Inc. (Jackson, MS).
Jerry Coder, president of EKC, said that his company has already frozen new customer agreements and limited existing customer orders to 12 weeks usage. He believes that customers may be able to achieve significant volume savings by optimizing their processes. For example, customers may be able to extend bath life rather than automatically replacing their bath chemistries on a set time schedule. In some cases, cleaning chemistries with lower concentrations of HAFB may still give satisfactory process results.
Coder explained that his company qualified BASF as a second source on May 10. EKC is working with a European customer to expedite evaluation of cleaning chemistries using the BASF-supplied material.
Alternative Products
Meanwhile, the shortage has opened the door for alternatives to hydroxylamine-based strippers. In the past, semiconductor fabricators have eschewed these products because they have not proven as effective.
Several options exist, says Wayne Cady of JT Baker Div. of Mallinckrodt Baker, Inc. (St. Louis, MO). The company says it is a leader in hydroxylamine-free cleaning chemistries for the semiconductor industry.
According to Cady, hydroxylamine cleans by reacting with plasma and ash residues to remove them. Alternative chemicals, he says, are gentler. They dissolve wafer residues and do a better job of protecting the substrate. Baker has two products that work by dissolution:
Baker Aleg-310. Introduced in 1996, Baker Aleg-310 solvent-based photoresist stripper removes polymers and ash residues. It is currently used for both bulk resist and ash residue removal.
Baker Rezi. Baker Rezi-28 and Rezi-38 aqueous ash residue removers do not contain SARA 313 listed components or hazardous air pollutants (HAPs), and have a less than 5% concentration of volatile organic compounds (VOCs).
Cady says the products offer cleaning performance comparable with hydroxylamine-based formulations, using the same equipment and materials under similar operating conditions.
Baker has launched a new program to expedite qualification and conversion of semiconductor manufacturing lines to its alternative cleaning chemistries. Under QuickQual, Baker will offer product samples, technical data, in-situ testing, and individual technical support to enable fabricators to pilot the products on their own equipment.
"The standard turnaround on qualifying and converting to a new cleaning chemistry is six to nine months or longer because of the planning that is required to minimize disruption of manufacturing steps before and after cleaning," says Cady.
"However, with a larger disruption upon them, we expect that manufacturers will want to slice that time drastically in order to continue production levels. QuickQual will allow them to perform many steps of the offline testing all at once, rather than sequentially."
New Technologies
Long-term resolution may ultimately come from other technologies, such as supercritical wafer cleaning fluids. Supercritical fluids are gases, most often carbon dioxide, liquefied under high pressure. When released from pressure, they turn into gases. The rapid change in physical state gives them exceptional solvating power.
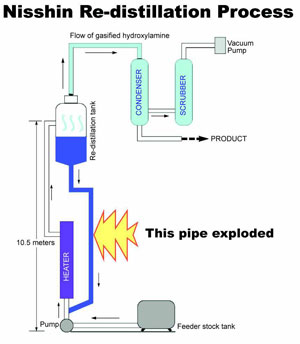
Recently, IBM licensed its supercritical wafer cleaning fluids technology to GT Equipment Technologies, Inc. (GTi, Nashua, NH). The company will collaborate to optimize the technology for next-generation semiconductor manufacturing processes. GTi will then market the technology to the semiconductor industry.
The IBM formulation uses supercritical carbon dioxide, modifiers, and cosolvents to clean wafers and remove residues. The system lets manufacturers clean wafers with minimal surface tension, critical in production of ultrafine-geometry circuitry. The technology also promises to reduce the use of ultrapure water and other expensive chemicals.
GTi also holds an exclusive license to supercritical fluid technology developed at the Los Alamos National Laboratory. The company specializes in the development of high-pressure equipment, and plans to become a leader in next-generation semiconductor cleansing materials and equipment.
For more information: EKC Technology, 2520 Barrington Court, Hayward, California 94545-3703. US Phone: 510 784.9105
For more information: J.T. Baker, 222 Red School La., Phillipsburg, NJ 08865. US Phone: 908-859-2151, Ext. 9204. European Phone: 31-570-687500. Asia Pacific Phone: 65-738-4333.
For more information: Heiko Moritz, Sales Manager, GT Equipment Technologies, Inc., 475 Amherst St., Nashua, NH 03063. Phone: 603-883-5200, Ext. 354. Fax: 603-595-6993.
By Alan S. Brown and Katherine Derbyshire