Genencor, Eastman Plan to Produce Ascorbic Acid, Other Chemicals From Corn
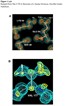
- Reichstein Comparisons
Eastman Chemical Co. (Kingsport, TN) and Genencor International, Inc. (Rochester, NY) plan to commercialize a new, low-cost route to ascorbic acid (vitamin C) that is among the first to combine biotechnology and chemical processing on an industrial scale. Genencor is taking a similar approach to develop a way to make polyester precursors for DuPont Co. (Wilmington, DE).
The ascorbic acid technology opens the door to new, wider use of biotechnology to make other chemicals. "We built a pathway to ascorbic acid," says Genencor president/CEO Tom Mitchell, "but we have the ability to add other enzymes to divert the synthesis toward other products. This proves that continuous biocatalysis is a viable and economic means to chemical synthesis."
"Obviously, not all chemicals can be made this way," says Eastman chairman/CEO Earnie Deavenport, "but a growing number will be and the combination of the two disciplinesbiotechnology and chemistrywill have a major positive impact on the economy and the environment."
The new aqueous-based ascorbic acid process uses simpler feedstocks, requires fewer processing steps, and eliminates organic solvents. Last year, Genencor and Eastman unveiled a similar but less efficient process that they said would cost half as much to build as conventional Reichstein-process ascorbic acid plants.
"Based on our analysis, we think it's more economical and more ecologically efficient than current processes for ascorbic acid," says Genencor technology development VP Karl Sanford. "We think the process can make money even at the low end of the price range for ascorbic acid."
He says ascorbic acid prices have fallen below $5/kg, from $15-17/kg three years ago, due to market share wars. Ascorbic acid has a global market of about $600 million.
Reichstein Comparisons (back to top)
The most widely used route to ascorbic acid is the Reichstein process. It starts with sorbitol, a reduction product of glucose, which it ferments. This yields ketogulonic acid, which the process then converts into ascorbic acid using a multistage chemical process.
"If you look at the Reichstein process, it generates a number of intermediates," says Sanford. "To preserve the chirality of ketogulonic acid requires blocking, deblocking, and cyclization steps because it is a linear molecule and ascorbic acid is a cyclic molecule. You need to close the ring in a way that preserves the chirality of the molecule."
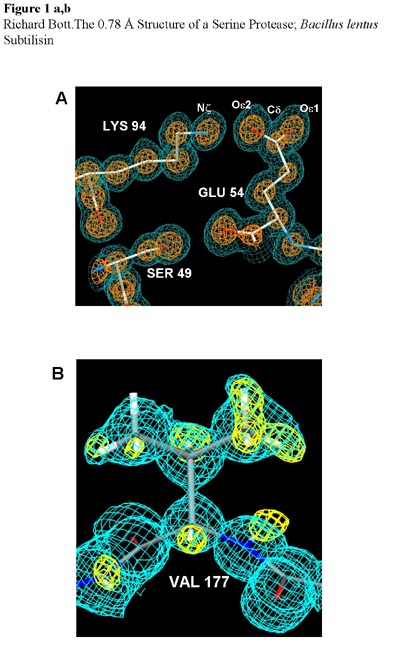
BASF, Merck KGaA and Cerestar have developed a cheaper route to ketogulonic. They plan to open a new joint-venture unit in Krefeld, Germany. Yet both this route and the Reichstein process require multistage fermentation and organic solvents.
The Genencor approach appears much simpler. It converts glucose, a sugar derived from corn, into ketogulonic, eliminating the need to make sorbitol. It then uses a combination of fermentation and chemical processes in aqueous media to convert the ketogulonic acid into ascorbic acid.
Sanford does not detail the downstream processing steps, but says the flow chart is significantly simpler than any existing commercial process. The substitution of water for solvents not only makes the technology greener, but yields "a seamless process that connects glucose to final processing," he says.
The technology is an improvement over the first-generation process technology described by Genencor and Eastman last year. At the time, the companies said the new route could compete economically with existing technology.
Since then, says Sanford, the company developed its aqueous processing technology. It also boosted the yield and speed at which its microbes convert glucose to ketogulonic acid. "Through metabolic pathway engineering, we've improved yield to way over 50% based on input of carbon," he explains. "We've achieved a substantial improvement in yield since last year."
"We have a joint-venture with Eastman, and our intent is to commercialize this process," he continues. While declining to provide specifics about plant size or startup dates, he notes that the companies plan another year of research before moving ahead with any plans.
ATP Consortium (back to top)
The project was launched four years ago by a five-company consortium under the National Institute of Standards and Technology (NIST) Advanced Technology Program (ATP).
ATP funds high-risk, high-payoff research. The award called for development of a continuous biocatalytic operating system. Sanford describes the existing system as somewhere in between a batch and continuous process.
In addition to Genencor and Eastman, the consortium includes the Electrosynthesis Co. (Buffalo, NY), MicroGenomics, Inc. (San Diego, CA), and Argonne National Laboratory (Argonne, IL). The five members received $15.6 million from ATP, which they matched with $15.6 million in their own funds.
Genencor, which is 50% owned by Eastman and 50% by Finland's Cultor Corp. (which in turn is owned by Danish manufacturer Danisco), provides the key genetic technologies for the ATP project. Eastman brings chemical processing discipline to the partnership.
Argonne provides both large-scale bioprocessing experience and such leading-edge measurement technologies as the advanced proton source and high-energy crystallography.
Electrosynthesis provides electrodialysis systems for recovery and purification of biochemicals. Microgenomics, an early-stage biotech startup, adds novel selection methodologies for enzyme discovery and modification.
"When we started the program, our goal was to create a continuous processes that would revolutionize the capital efficiency of running these processes," he explains. "Our intent was to create some generic methodologies, tools, and paradigms that we can bring from ascorbic acid to other programs either individually or in other partnership with other companies."
Genencor wants to apply those tools to make other chemicals and food additives, says Sanford. "President Clinton is calling for greater development of biobased industrial products. We see an opportunity to come up with better enzymes to recombine biomass building blocks such as glucose and C5 sugars into other products. We're looking for opportunities where the combination of genetic engineering of metabolic pathways and green chemical processing technologies open new doorways."
Polyester Precursors (back top )
Genencor is also in the fourth year of a project to make polyester precursors for DuPont. Most commercial polyester routes are based on 1,2-ethanediol (more commonly known as ethylene glycol), Sanford explains.
Researchers have long known that the extra carbon unit in 1,3-propanediol (PDO) provides some useful properties, but they have not found an economic route to make it. The program's goal is to find a cost-effective biotech/chemical route to 1,3-propanediol. Sanford describes the program as "on track."
Genencor was founded in 1982 as a collaboration between Genentech and Corning, Inc., and soon cloned the first recombinant organism designed specifically to produce industrial enzymes. Eastman invested in the company in 1987, and became co-owner with Cultor in 1994. Genencor became a large-scale producer of industrial enzymes when it opened its Cedar Rapids, IA, plant in 1991. It acquired the industrial enzyme businesses of Royal Gist-Brocades in 1995 and Solvay SA in 1996.
For more information: Karl Sanford, VP, Technology Development, Genencor International, Inc., 925 Page Mill Rd., Palo Alto, CA 94304. Phone: 650-846-7584. Fax: 650-845-6507.
By Alan S. Brown