Electromagnetic pipeline inspection widens its scope
Can chemical plant applications be far behind?
The need for ongoing pipeline corrosion monitoring is apparent. Profile says piping problems cause 95 percent of all failures in chemical plants, refineries, natural gas transmission lines, and utilities. Ongoing monitoring also makes good economic sense, since it lets companies respond to a real maintenance needs rather than schedule expensive periodic examinations of entire pipeline systems.
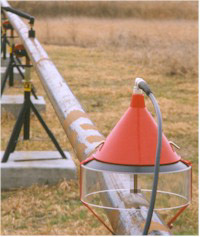
An electromagnetic wave test in progress.
Electromagnetic waves promise both accuracy and low costs. During the past three months, Profile conducted a series of confidential field tests of its dual pulse propagation analyser (PPA) with New York utilities. The tests show the technology is able to inspect underground pipelines for external corrosion, by accessing these lines solely through utility test leads, buried under every city street.
"The field tests have proven definitively that we can now evaluate up to about 75m of buried piping in one measurement setting," said Profile vice chairman(technology) John Kuo. "Two years ago, we could only measure 15m of a pipeline in one measurement setting, and our next immediate goal is to expand our inspection range to 150m and longer. Presently, there is no other comparable technology available in the industry."
The results are especially impressive, according to Kuo, because the dual pulse system is able to accurately assess corrosion in NYC's complex subsurface environment using only conventional utility test leads. The company can routinely measure pipe segments longer than 150m in less complex environments, such as those surrounding chemical plants and refineries.
Kuo calls the field tests "a breakthrough with significant implications. What this means, is that we can now offer the entire utility sector a low-cost, non-invasive, corrosion testing technique, which will potentially save the industry millions of dollars each year in costly dig-ups, while increasing protection against unexpected pipeline failures."
Dual pulse electromagnetic wave inspection provides 360-degree non-invasive corrosion testing of insulated, buried or inaccessible pipes. It provides global evaluation of piping segments or detailed detection of external corrosion. Engineers do not have to remove insulation, dig up below-grade piping, or even take the pipe out of service to inspect it.
The system uses a multi-channel generator to send a broadband electromagnetic pulse along the surface of a steel pipe. Each frequency that comprises the pulse has its own complex propagation constant, which is a function of the pipe's electromagnetic properties. When the electromagnetic waves travelling down a steel pipe encounter corrosion at any point around the pipe's circumference, they become distorted. Profile's software analyses the distorted signal, to pinpoint the corroded area.
The company transports the system to remote locations in a small field van. It needs access only to the ends of the segment to conduct the test. The company magnetically attaches pulse generators on both ends of the pipe, either by cutting through the insulation or using a flange hub or other protrusion. It positions a receiver adjacent to one of the pulsers.

Electromagnetic wave distortions indicate corrosion.
It then excites both ends of the pipe with two synchronised electromagnetic pulses. By controlling the delay between the first and second pulses, engineers can determine the precise location where the pulses meet.
Analysing the interference pattern caused by intersecting pulses shows Profile whether corrosion exists at that location. By varying the delay between the signals, Profile can sweep the entire length of the pipe for signs of corrosion. The company has also developed a second technique, single-pulse or CBZ (antenna calibration mark-Z).
Either technique allows it to determine the overall integrity - from good to severely corroded - of a piping segment up to 150m in length. Both systems are capable of detecting corrosion at any point on the pipe's circumference, and pinpointing it to within around 0,66m above ground, and around 1,5m below ground. Profile says its global inspection approach allows companies to rapidly rank piping and concentrate further evaluation on the most seriously damaged pipes first.
Alan S. Brown
Provided by: RPP Pipe Supports & Bellows Pty Ltd.