DuPont, Fluor to Deliver Process for Polyester Packaging Resins
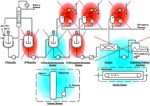
The polymerization process is the first technology specifically developed for packaging resins, says DuPont Polyester Technologies managing director Robert G. Hirsch. "We fully expect it to be the process of choice for global resin production."
According to Hirsch, the process meets or exceeds DuPont's original development targets for significantly decreased investment, lower operating costs, reduced emissions, and improved product quality.
NG-3 Technology
NG-3 is a significant departure from conventional polyester technology. Rather than relying on a melt plant to produce an intermediate with a high intrinsic viscosity (IV, typically around 0.6- 0.65), NG-3 produces a low-IV oligomer intermediate. It then carries out most of the polymerization in the solid state.
Other PET producers have attempted to form low-viscosity oligomer droplets in the past. They failed because the IV of the oligomers was too low, and the particles did not form droplets of consistent size and shape. Because the particles lack structural integrity, they are difficult to handle and abrade easily during handling. This generates fines that interfere with downstream processing. While producers can anneal particles to increase crystallinity and durability, it adds time, capital, and cost to the process.
DuPont says it has solved the problem with technology that produces robust droplets from low-molecular-weight oligomers with a degree of polymerization (DP) of only 20-30. Although the company does not say how it imparts crystallinity to its polymers, its patent, Process for forming crystalline polymer pellets (US Patent 5,744,074, April 28, 1998), describes the rapid transfer of droplets to a heated conveyor system as a means of crystallizing oligomers.
DuPont says the way it forms particles imparts a crystalline structure that gives them the strength to stand up to further processing in the solid state polymerization (SSP) unit. (It says composition of matter patents cover the crystalline structure of NG-3 intermediates and final products.) The ability to rapidly crystallize the pastilles reduces the equipment and time needed to condition the particles prior to sending them to the SSP.
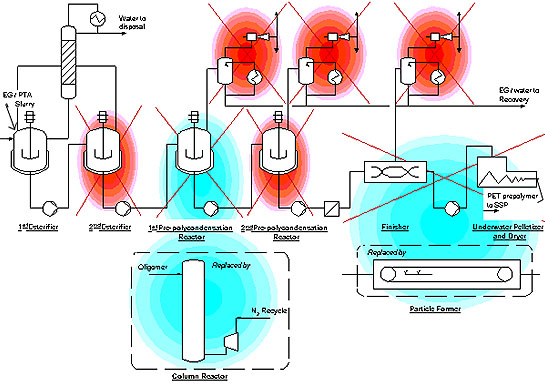
Environmental Benefits
Another important NG-3 advance lies in its patented prepolymerizer. A countercurrent reactive distillation column, it increases the degree of polymerization using a closed-loop nitrogen circulation system.
Conventional prepolymerizers typically operate at reduced pressure. They require vacuum systems to remove and recycle excess ethylene glycol (EG, which is used in the polymerization process), as well as remove diethylene glycol and other degradation byproducts. The process is problematic to control for high efficiency, and the vacuum sources themselves may emit organic volatiles into the environment.
A DuPont patent, Process of making polyester prepolymer (US 5,786,443, July 28, 1998), describes a nitrogen-driven countercurrent prepolymerizer that operates under slight pressure. It eliminates the need for a vacuum system. Instead of drawing off excess EG in vacuum, it continuously feeds terephthalic acid into a reactor operating at 24.7-189.7 psia and 200° C.
At the same time, it slowly adds EG, which reacts with the terephthalic acid for at least 15 sec to produce a prepolymer with a 2- 7 DP. The reaction product is passed through a heated pressure- reducing device at the top of the reactor. At the same time, DuPont feeds a chilled nitrogen stream up from the bottom of the reactor at a low enough flow rate to give it a reactor residence time of at least 2 min.
Chilled polyester (DP=10-30) exits the bottom of the reactor. At the top of the reactor, heated plates flash off excess EG, water, low- molecular-weight solids, and other volatile condensation products. They leave with the rising nitrogen stream. DuPont recycles EG to the slurry preparation area and purges the water. There is no unplanned EG release through the vacuum system.
Another valuable feature of NG-3 is a substantial reduction in melt phase residence time. PET degradation is a function of time and temperature in the melt phase, says DuPont. NG-3 residence times are less than 2 hrs, only one-third to one-half as long as conventional technologies. This results in significantly less product degradation and improved product quality.
Economics
DuPont says NG-3 plants 200,000 mt/yr or larger will produce a higher-quality polyester container resin at significantly lower investment than possible with current technology. It says demand for PET resins, used to manufacture soft drink, cosmetic, medicine, and food containers, averages double-digit growth annually.
DuPont and Fluor plan to initially focus on licensing the new technology in Asia, where demand for PET packaging is rising fastest.
"We are very pleased to be ready with this technology and the alliance with Fluor at a time when the polyester industry is returning to health," adds Hirsch.
While the two companies have worked together before, the NG-3 alliance marks the first time they will share the cost of researching and developing a new technology.
"DuPont and Fluor bring complementary strengths to the partnership," says Hirsch. "In addition to the basic technology, DuPont provides operating and technical know-how, broad-ranging technical services, and licensing rights under our extensive patent portfolio. Fluor will provide proprietary engineering, construction, and operations services to deliver the technology to manufacturing licensees in the most cost-effective fashion.
"This unique combination of effective technology and world-class engineering will allow us to build the most cost-effective resin plants now and evolve to even higher-scale, lower-cost plants, employing the latest information technology, in the future," says Hirsch.
Fluor Corp., with 1999 revenues of $12.4 billion, provides services on a global basis in the fields of engineering, procurement, construction, maintenance and operations, equipment leasing, consulting and coal production. It has headquarters in Aliso Viejo, Calif. and operates in 45 countries with 50,000 employees.
Details: Fluor Daniel, Inc., 3353 Michelson Dr., Irvine, CA 92698. Phone: 949-975-2000. Fax: 949-975-5271.
By Alan S. Brown