Corrosion inhibitors — An overview
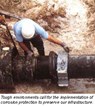
Contents
Surface Preparation
Coating Films
Flash Rusting
Formulating Parameters
About the author
The Coatings Encyclopedic Dictionary (CED) defines corrosion as "the deterioration of metal or concrete by chemical or electrochemical reaction resulting from exposure to weathering, moisture, chemicals, or other agents in the environment in which it is placed." Clive H. Hare did an in-depth study on this subject and published it in FSCT Unit #26 titled: "Corrosion and the Preparation of Metallic Surfaces for Painting," which is worth a review by any formulating coating chemist.
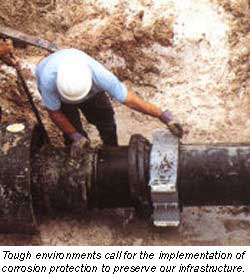
As an overview, this article "tours" several aspects of corrosion.
We have always known that in process of rusting, one volume of steel yields 20 volumes of rust. Coatings chemists formulate maintenance paint and high performance coatings to protect these reactive surfaces from airborne industrial pollutants, humidity, condensation, chemical fumes, marine and high moisture environments. Formulated paints are applied to bridges, storage tanks, silos, steel structures, piping and equipment.
In some cases unformulated "overbased calcium sulfonates" prevent rusting when applied as is to steel surfaces.
Specialty coatings prevent rusting by displacing moisture and adhering tenaciously to a given substrate.
There are two main mechanisms of paint protection, barrier and galvanic.
- Barrier protection: As the name indicates, the coating film forms a barrier offering resistance between environment and material. This has been the conventional method. It is required that the coating film is continuous and uniform, with no pinholes, skips or breaks.
- Galvanic protection: Also known as sacrificial protection. This is the mechanism used in the "dip" type galvanized coating for steel. The coating formulation is said to be zinc-rich, with about 85 to 95% Zinc metal by weight. In the process, the "galvanic cell" principle is used. Here, water from rain, moisture, dew acts as an electrolyte, zinc at the anode and iron at the cathode fills the functional requirements of a galvanic cell. Electric current will cathodically protect the surface from corrosion. Zinc is corroded and wasted away in process and hence the term "sacrificial protection". Since protection is accomplished by electrical means, it is not essential to have a pinhole free coating. Further, if the topcoat over the zinc rich primer is breached, no corrosion should result.
Surface Preparation (Back to Top)
Success of any given coating depends on how well the surface is prepared. Preparation requirements vary depending on coating type, substrate conditions i.e. new or painted, if painted the type of paint — oil or waterborne and the exposed environment — mild or severe. If mild, remove loose rust and use a primer. If severe, sandblasting is recommended. Note that surface preparation is very critical when waterborne coatings are used since the coating will not wet the oil. Fairly clean surface is acceptable for solvent-based paints.
Coating Films (Back to Top)
A good rule of thumb is to apply a minimum of 5 mils (dry) in a minimum of three coats. For primers, 1.0 to 1.5 mils film thickness is adequate. Since film loss will occur with time due to chalking, weathering, service condition and mechanical abrasion, as a preventive maintenance, one must maintain 5mil dry film thickness by repainting and periodically measuring film thickness.
Flash Rusting (Back to Top)
Exhibition of small brown rust spots on light waterborne paint is termed as flash rusting, which occurs during the drying phase, when waterborne paint is applied to a ferrous substrate. Light colored coatings can become dark. This is more prevalent in polyvinyl acetate formulations than with acrylics. This occurs due to slow drying process of the paint film and dissolved oxygen in the paint reacting with high humidity in atmosphere. We know that amines maintain basic conditions during drying and salts, via anodic and buffering actions, maintain basic side in films.
So to control flash rusting, add about 0.5 to 1.0 pound per gallon of rust inhibitive pigment, such as Zinc Hydroxy Phosphite, or Molybdenum or Zinc Phosphate. Alternatively 0.25% of any one of the following is also found effective: Ammonium Benzoate, Sodium Benzoate, Sodium Nitrite, Potassium Nitrite, Sodium Phosphate, Amino Methyl Propanol (AMP) or Morpholine.
Formulating Parameters (Back to Top)
Some points to remember while formulating rust inhibitive coatings are:
- Styrene Acrylics offer very good resistance to acids.
- Aromatic Hydrocarbons, Ketones and Esters soften coating films.
- Latex that crosslinks upon drying offers excellent protection.
- Slight water solubility of Corrosion Inhibitive Pigment, as in Barium Metaborate (0.3 to 0.4% solubility in water) is preferred. Metaborate B2O4 anions complex with iron or other cations.
- If the corrosion inhibitive pigment portion of the formulation is too soluble, latex systems will shock.
- Use water immiscible coalescing agents.
- A good corrosion inhibitor is one that has minimum water sensitivity.
- Use the minimum possible volume of surfactant, allowing for adequate stability.
- Remember that Lead Silicocromate and Strontium chromate are banned and should not be used as corrosion inhibitors, even on the small chance that they are available.
- Zinc Hydroxy Phosphite, Zinc Phosphate, Calcium Borosilicate, Calcium Zinc Molybdate, Precipitated grade – slightly basic Calcium Carbonate and Zinc Oxide (French process grade – very reactive – use low levels) are but a few corrosion inhibitive pigments used by our industry.
- Styrene Acrylics is good for corrosion resistance. Polyvinyl Acetate and Vinylidine chloride is marginally effective in latex category.
- Silica blisters less over steel.
- Micaceous Iron Oxide's platelet structure reduces moisture transmission through film.
- Red Oxide is low cost.
- Disodium Oleamide Sulfosuccinate, Amino Sulfonate, Alkanolamide and organic phosphate esters are also used as corrosion inhibitors.
I hope this brief overview serves as a good reference to newcomer coating formulator chemist and to old timers to optimize their existing formulations.
About the author (Back to Top)
Ashwin V. Parikh, manufacturing/process domain expert with VerticalNet, Horsham, PA, is a chemist and chemical engineer with a MSIA degree (Master of Science in IndustrialAdministration.) He has held various positions at Glidden-ICI, Union Carbide, Coulter Electronics, Buckman Labs, and Witco Corp. in the areas of technical sales training, distribution management and customer support. Parikh has also addressed the FSCT (Federation of Societies for Coating Technology) numerous times on coatings technology.