Brewery Sings Praises of Nondispersive Diffusion For Nitrogenation
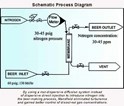
The beer maker switched to hollow-fiber nondispersive diffusion system to introduce nitrogen into its beer-making processes. The approach reduces turbulence, lowers costs, and improves its overall control over dissolved gas concentration when compared to conventional direct injection alternatives.
In addition to nitrogenation, the membrane has been used for ultrapure water deoxygenation and decarbonation; boiler feed water degassing; and process water deaeration and carbonation.
The nondispersive diffusion system features a Liqui-Cel Extra-Flow Membrane Contactor manufactured by Celgard LLC of Charlotte, NC. The unique, high-efficiency contactor, featuring a hollow-fiber contact medium, has been used to transfer a variety of dissolved gases, to or from an aqueous stream, in a variety of applications in the food & beverage, semiconductor, power, chemical, and pharmaceutical industries.
Creating A Sooth Brew
At the Mansfield Brewery, the market-driven purpose of nitrogen introduction was to lower CO2 content, which was necessary to create a "smooth" beer — a "keg" beer that would mimic "cask-conditioned" beers, but without losing the "head" characteristic of keg beers.
Mike Cleator, the brewery's chief engineer, recalled that dispersive direct-injection technology already available for nitrogen introduction was considered disadvantageous.
"Direct injection would have introduced highly undesirable turbulence that would have knocked CO2 out of solution," he explained, "because in order to make the nitrogen dissolve with any speed, pressure would have to be raised up to 8-9 bar (132 psi). With the Celgard technology, nitrogen could be introduced at low pressure — typically 30-45 psi — a level that is actually lower than the 60 psi pressure we need to move the beer around."
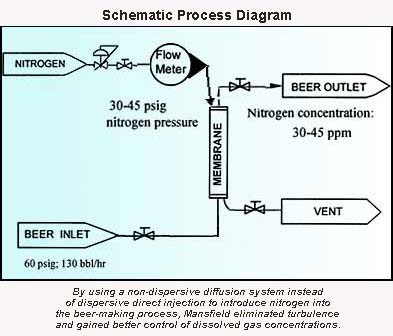
Cleator added that capital cost savings were a significant advantage for the installed system, which has been performing well.
"The cost for the non-dispersive nitrogen diffusion system, consisting of the Celgard membrane, an Orbisphere 2-channel CO2/N2 meter, a control panel, and a membrane cleaning tank with pump & heater, came in at about $64,000," he stated. "By comparison, off-the-shelf cost for a dispersive direct-injection system would have been about $144,000. We've now been operating successfully since May 1997 overall, and since December 1998 with a revised membrane cleaning operation that has boosted production levels."
Process Control Advantages
In addition, he said there were important process control advantages.
"The nitrogenation pressure is very easy to control — we don't need extra pumps to raise the pressure, and then valves to slowly reduce it," he noted. "And avoiding the reduction of beer pressure over valves takes away the associated risk of inducing CO2 breakout. Overall, this method offers considerably more flexibility as a processing tool than straightforward injection would, especially regarding control of CO2 content."
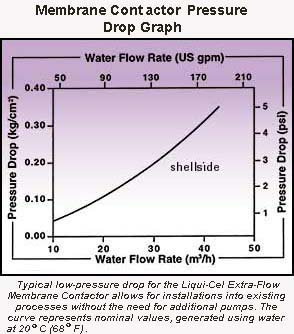
Cleator elaborated that he can't allow water and CO2 to build up on the nitrogen side of the membrane. Because of CO2 and nitrogen partial pressures, he needs to keep increasing the nitrogen, but can't exceed the beer pressure. So he has a continuous purge of gas from the lumen side of the membrane that removes the water vapor and sweeps out CO2.
Per Henry's Law, he continued, dissolved oxygen content of the beer is reduced as it goes through the membrane. With mixed gas placed on the membrane, Henry's Law also allows adjustment of CO2 content at the same time as nitrogenation. The amount of CO2 that gets removed is proportional to the amount of nitrogen sweep gas purged out.
"If the beer is too high in CO2, the traditional remedy is to purge it by injecting nitrogen, thereby shocking it out of solution," he said. "But this is very inefficient, wasting nitrogen, and also very messy, with lots of froth coming out of the vent and all over the floor, typically at the same time the Chairman is walking around. Alternatively, you just increase the nitrogen sweep rate, increasing CO2 through the membrane, and reducing CO2 concentration to within specification."
Conversely, he pointed out, a lower CO2 level can be raised to within specification by introducing a mix of CO2 and nitrogen on the gas side of the membrane. This allows for nitrogenation and carbonation at the same time, with typical CO2 concentration at 2-2.5 g/l.
Membrane Cleaning
Regarding membrane cleaning, which is needed after each use, Cleator said the cycle includes water rinse to remove beer residue, followed by 2% NaOH for 1/2 hr, then cold water rinse for 10 minutes, and finally 600 ppm sulfite KMS (potassium meta-bisulfite) sterilizing solution, which is circulated and then left full on the membrane until the next use.
"We were initially disappointed that the membrane had to be left full of sterilizing solution after a run and rinsed out before the next run," he recalled. "But we found this could be automated, with push-button initiation of the cleaning sequence beginning with water entering to flush out the sterilizing solution."
Cleator noted he initially wanted to use the 2% NaOH at 10- 12°C (40-54°C F), instead of at 30°C C (86°C F) as recommended by Celgard, because of concern about the presence of hot caustic.
"But that resulted in some liquid wetting through into the gas, or lumen, side of the membrane," he said. "Consequent reduction in membrane performance was realized as lower nitrogen in the beer. In order to achieve the 30-45 ppm nitrogen level desired, it was necessary to reduce the beer flow rate from 120 barrels/hr to 50 barrels/hr, which caused packaging management to go into sense-of- humor failure."
Cleator reports that when he started using the NaOH at the higher temperature, he readily raised production up to 120-130 bbl/hr, with frequency of cleaning not a problem.
"Cleaning is done four times a week only because we are running different types of beer," he said. "If we were running it all in one day, we would only need to clean it once. And we've been very happy to see that upon cleaning, the membrane has always returned to its original installed condition and performance. It does now take two hours to heat the NaOh vs. one hour previously. But should this later be deemed a problem, we could simply replace the current tank immersion heater with a steam heater."
Operating Costs Under Control
Regarding operating costs, Cleator said "it's all in the detergent," which he notes is relatively inexpensive because it must be a chlorine- free crude form. He said that before establishing proper cleaning technique, prefiltration costs had been high due to changing filters once a week, but they now are changed only every 6-8 weeks. Each change of the 10-micron pore size filters costs $480 and lasts for 8,000 barrels of production.
As for ease of operation, he said special expertise was not required.
"The lads in process operations can easily handle it," he said. "When they start a runoff, they stand by to make sure it reaches a steady state within 5-10 minutes, then go away and do other things and check every 1/2 hour or so. And we didn't need to put in any fancy automation. If we moved into very large production, we would do that, but not with any great difficulty. The plant is already run by a small PLC. To include this cleaning operation in the automation, we would just put in a control valve linked to the output of the now manually-set nitrogen meter."
In conclusion, Cleator suggested that the experience has also paid qualitative dividends.
"We were excited about the opportunity to use a new technology, and to be the first to apply it commercially in our field," he said. "And it was gratifying to be taken back to first principles learned in school days, and to have to use science to think for yourself. We've also received good technical backup from Celgard throughout the experience, from Paul Peterson and plant personnel in Charlotte, and Jurgen Schneider in their Wiesbaden office. Both locations have been readily available at the end of a telephone or e-mail."
Patented Design
Celgard's Liqui-Cel Extra-Flow Membrane Contactors have been performing commercially since 1991. The patented design contains microporous polypropylene hollow fibers knitted into an array that is wound around a distribution tube with a central baffle. The hollow fibers are arranged in a uniform open packing, allowing for greater flow capacity and utilization of the total membrane surface area.
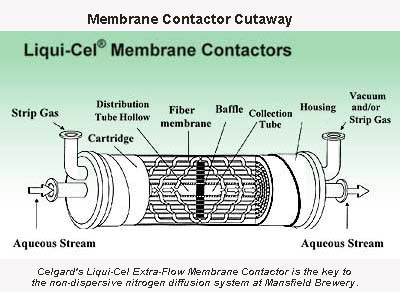
During operation, an aqueous liquid flows over the outside of the hollow fibers, with the patented design forcing it radially across the array. A strip gas or vacuum, separately or in combination, is applied on the inside of the hollow fibers. Because of its hydrophobic nature, the membrane acts as an inert support, allowing intimate contact between gas and liquid phases without dispersion.
The interface is immobilized at the pore by applying a higher pressure to the aqueous stream relative to the gas stream. As the aqueous stream flows over the outside of the fibers, the strip gas or vacuum flows countercurrent inside the hollow fibers. The result is fast diffusive transfer of dissolved gases from or to the liquid phase.
For more information: Celgard LLC, 13800 South Lakes Drive, Charlotte, NC 28273. Phone: 704-588-5310. Fax 704-587-8585.
Edited by Bill Noone and Alan S. Brown