Albemarle Will Do Custom Fluorinations Using New Halex Technology
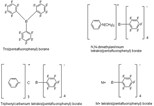
Albemarle, which uses the technology to manufacture boron cocatalysts used in single-site ("metallocene") polymerization, wants to provide custom halogenation services for chemical manufacturers. Fluorination is commonly used to synthesize agricultural chemical and pharmaceutical intermediates.
The company is well positioned. It says it is the world's largest producer of single-site catalysts and aluminum alkyls. It just completed a 50% expansion of an aluminum alkyl plant to make methylaluminoxane (MAO), which is also used as a cocatalyst for single-site synthesis.
The new halex chemistry is specifically geared toward difficult fluorinations, such as attaching multiple fluorines and fluorinating difficult-to-reach positions. According to research manager Hans Van Beek, the company typically achieves yields of 85-95%. The company estimates this is as much as two to three times higher than current processes. "No one is waiting for you if you're not better than what's already out there," says Van Beek.
Albemarle has already demonstrated the process. It produced 20 mt of a highly fluorinated aromatic during an initial halex run in a 2000 gal multipurpose reactor at the company's Baton Rouge process development center in the spring of 1998. It implemented additional process improvements prior to a second 30 mt fluoroaromatics campaign in the second quarter of 1999.
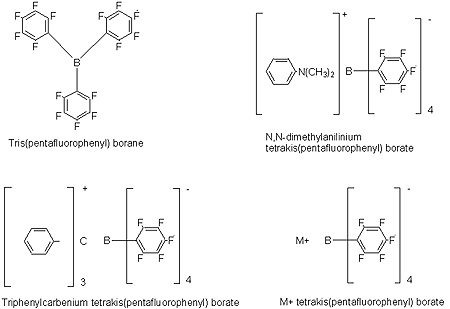
The multipurpose unit could make 400 mt/y if it ran year-round. Albemarle also says it could modify its South Carolina plant for halex, and bring a commercial plant on stream by 2000 or 2001 if demand warranted. The commercial unit would be capable of making several halex-fluorinated aromatics.
Halex Chemistry
Halogen exchange reactions are one of several methods developed to circumvent problems with direct fluorination. "Direct fluorination doesn't work," says Van Beek, "because you don't end up with the substitution you want. Instead, the heat of reaction can tear the molecule apart."
Controlled fluorination involves what Van Beek calls "tricks." One common approach is to add a diazo group (N2), then in a subsequent reaction, substitute it with hydrogen fluoride, hydrogen tetrafluoroboride, or sodium tetrafluoroboride. Halogen substitution is another trick. In involves controlled chlorination, then replacement with fluorine.
Halex has been carried out for years by reacting chlorinated aromatics with such alkali metal fluorides as potassium fluoride, rubidium fluoride or cesium fluoride. The reaction takes place above 400 C (or at 200-230 C if using an aprotic solvent such as sulfolane). Even though producers may catalyze the reaction with quaternary ammonium salts, metal carbonyls, crown ethers, or cryptates, the reaction is still slow.
Worse, the reaction has fairly low yields of polyfluorinated aromatics. A typical halex route to fluorinated boron metallocene cocatalysts, for example, would start with hexachlorobenzene and potassium fluoride. It would typically yield hexafluorobenzene (the desired end-product) as well as a mixture of chlorofluorobenzenes coproducts.
Albemarle is mum about the exact chemistry involved. It has, however, received several patents pertaining to halex chemistry. These include Halogen exchange reactions (US 5,824,827, Oct. 20, 1998) and Catalysis in halogen exchange reactions (US 5,965,781, Oct. 12, 1999).
The former describes an anhydrous alkali metal fluoride-haloaromatic mediated with an aminophosphonium catalyst, such as tetrakis(diethylamino)phosphonium bromide. The second patent describes a treatment to improve the efficiency of tetra(dihydrocarbylamino)phosphonium halide, a halex catalyst.
The company will not comment on the relevancy of the patents. It does note that it has received many patents and has filed many more patents involving fluorine.
Reactions
Meanwhile, Van Beek is happy to discuss what the company's new halex technology can do. The company's approach allows it to fluorinate many substrates, position multiple fluorines on the molecule, substitute fluorines, and leave a halogen in position for latter substitution to yield pentafluorobenzene, bromopentafluorobenzene, or alkyl pentafluorobenzene (see image).
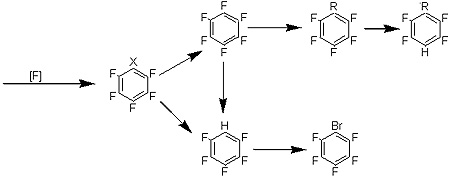
Conventional halex technology can usually attach the first two fluorines, but finds it much more difficult to achieve substitution in the meta position. Albemarle has demonstrated the ability to fluorinate the meta position. "When you want to attach fewer than five or six fluorines, our technology gives you better selectivity than with conventional halex catalysts," says Van Beek. "We see higher yields, better reaction conditions, and better selectivities."
For more information: Hans van Beek, Research Manager, Albemarle Corp., 8000 GSRI Ave., Baton Rouge, LA 70820. Phone: 225-768-6004. Fax: 225-768-6161.
By Alan S. Brown