ACS Award for Shell Process Underscores Growing Excitement in 1,3-Propanediol, PTT
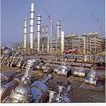
PDO is a key intermediate in Shell's Corterra polytrimethylene terephthalate (PTT) polymers. PTT has broad application as an engineering thermoplastic and spun fiber or yarn in carpeting, textiles, apparel, and nonwovens. In carpets, it combines the chemical and stain resistance of polyester with the elastic recovery (wear resistance) of nylon. In textiles, it provides stretch, comfort, and easy care.
Although PTT was first developed in the early 1940s, it took Shell's continuous ethylene oxide (EO) hydroformylation process to make it economical. The award serves to underscore the growing excitement around PDO and PTT chemistry.
Shell's PDO Route
Shell's involvement with PDO dates back to the early 1960s, when it began producing the intermediate by acrolein hydration. Cost and product quality concerns drove the company to abandon the process and seek other routes. EO hydroformylation appeared attractive, but proved difficult to master. The company eventually put development on hold until the early 1990s, when a breakthrough in hydroformylation catalysts rekindled interest.
The Shell PDO process uses a cobalt-based catalyst to catalyze hydroformylation of EO and synthesis gas in solvent. This yields some PDO and 1,3-hydroxypropanol (HPA), an intermediate that Shell recovers through water extraction or evaporation.
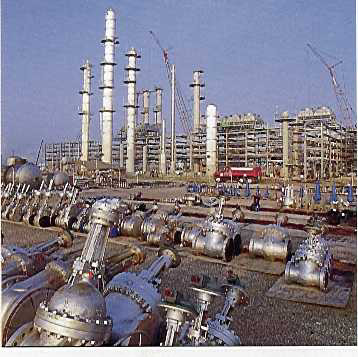
Shell then hydrogenates 3-HPA in a fixed-bed reactor at 75-150 bars and 100-200 C. Distillation to remove water and impurities yields a fiber-grade feedstock. Shell produces PDO at a new plant in Geismar, LA. The unit supplies Shell's Point Pleasant, WV, PTT facility, whose capacity tripled to 45 million lb/y in July 1999. Shell has also announced plans to open a 250 million lb/y PTT plant in Mexico in 2001.
Competing Routes
Shell's technology is not the only route to PDO. Degussa AG (Frankfurt, Germany) and DuPont (Wilmington, Del.) are partnering on a propylene-based process. DuPont acquired the technology from Degussa in April 1998 and opened a 20 million lb/y PDO plant in Wesseling, Germany, four months later.
The process catalytically converts propylene to acrolein, which it then hydrates to form HPA. A fixed-bed reactor converts the latter to PDO. Distillation yields a fiber-grade product. DuPont uses PDO to manufacture its 3GT PTT in two small plants in Kinston, NC, and Dumfries, Scotland. DuPont says it is considering building a 100 million lb/y PDO plant on the US Gulf Coast.
The Degussa route is not DuPont's only option. It has linked with Genencor International, Inc. (Rochester, NY) to develop a biotech pathway to PDO. It uses genetically modified microorganisms to convert corn-derived glucose into glycerol, which is aerobically converted to HPA and then PDO. The companies plan to build a 400,000 lb/y pilot plant in 2000.
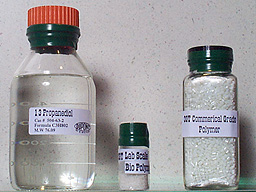
Shell key advantage over DuPont-Degussa technology is its lower capital costs, since it eliminates a process step (propylene to acrolein). Its process uses inexpensive syngas and EO, where Shell is a strong producer. DuPont's route, on the other hand, starts with a lower cost raw material, propylene.
PDO has other uses in addition to PTT. Shell is positioning it as a formulation alternative to 1,4-butanediol (BDO) and other diols. Potential uses include paints, composites, adhesives, laminates, UV- cured coatings, solvents, and antifreeze.
Researchers Honored
In addition to developing a new route to PDO, Shell's research team also developed the process to manufacture PTT polymers. They also worked with selected customers to help engineer processes for making carpet, textiles, and other PTT products.
The members of the PDO Development team included:
- Joseph Powell, staff research engineer responsible for the PDO technology enhancement and commercial process start-up for Corterra Polymers. His major accomplishments also include development and commercialization of bisphenol-A technology.
- Paul Weider, staff research chemist for the New Chemical Portfolio Development, the group charged in 1990 with finding a new core business that eventually developed Corterra Polymers. He is working to identify and develop new business opportunities and support for growing ventures at Shell.
- Hoe Chuah, senior staff research scientist and technical leader responsible for the Corterra Polymers. Branded Carpet Fibers commercial development. His research has included the study and properties of oriented polymers, high performance engineering thermoplastics and thermosets.
- Donald Kelsey, staff research scientist and senior chemist on the team developing the process (synthesis) chemistry for Corterra Polymers, including the development of commercial process and fundamental chemistry research related to catalysts, stability and by-product formation.
- Juan Arhancet, formerly the research engineer in charge of new chemical product development. He worked on research and development on hydroformylation and hydrogenation.
When ACS presents the award at its March 2000 meeting in San Francisco, it will mark Shell's second major award for the technology. In 1998, Powell won the Arthur Dehon Little Award for Chemical Engineering Innovation from the American Institute of Chemical Engineers (AIChE). The award is present once every three years.
The team has more than 50 current and pending patents and a number of published papers, both important considerations for the ACS Award for Team Innovation. The Corporation Associates of the American Chemical Society sponsor the award to showcase multidisciplinary technical teams that have transformed innovative ideas into commercial products.
For more information: Corterra Fibers, Shell Chemical Co. PO Box 2463, Houston, TX 77252-2463. Phone: 713-241-8230 or 888-267-8377. Fax: 713-241-2438.
By Alan S. Brown