Podbielniak Contactor: A Unique Liquid-Liquid Extractor
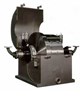
B&P Process Equipment and Systems
Introduction
The Podbielniak Contactor, popularly known as the "Pod," is a liquid-liquid centrifugal extractor and separator (figure 1) providing differential countercurrent extraction in a compact hermetic rotor. It provides up to 5 theoretical stages in one unit and can separate liquids with a specific gravity difference as low as 0.01. Used successfully for more than fifty years to solve extraction problems in the chemical process industry, the Pod has a bright future in new technologies as indicated by ongoing research in non-conventional applications.
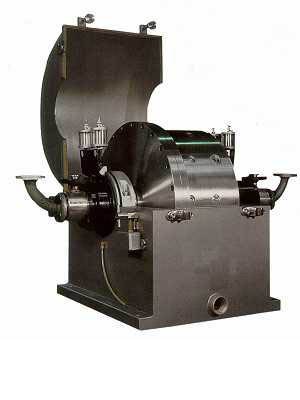
This paper covers mechanical and operational features of the Pod, its advantages, along with its various applications illustrated by typical examples.
Process Fundamentals
The Pod operates on two principles: separation and extraction. Separation effectiveness is a function of the density difference, separation force, and the residence time at that separation force. In a centrifuge like the Pod, the centrifugal force creates a separation force many times normal gravity, denoted by Xg. As the Xg force is increased, lower residence time is required for a given separation. The process in which a component is removed from one solvent by contact with another immiscible solvent is called extraction. An optimal solvent has a high distribution coefficient, meaning the solute favors the solvent phase many times more than the feed phase.
Mixer-settlers are the most basic equipment for extraction. Typically, mixer-settlers have low efficiency, long settling time, require a lot of space, and are labor-intensive. Another extraction device, sieve plate column, is also known as perforated tray tower. As seen in figure 2, it is a cylindrical column with perforated bands that act like multiple countercurrent mixer-settlers. Liquids are forced countercurrently through the perforations, leading to intense contact between the two liquids and generation of interfacial surface area for mass transfer.
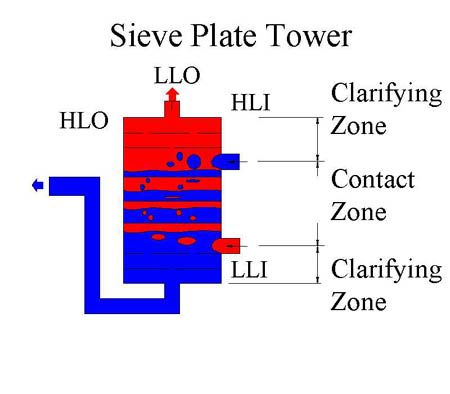
The Podbielniak extractor is analogous to a sieve plate column that is rotated about the top. In other words, the height of the sieve plate column is equivalent to the radius of the Pod. Multiple Xg force allows generation of a large interfacial area in a fraction of the sieve plate tower's volume. The Podbielniak contactor has perforated cylindrical bands that serve the same purpose as the horizontal plates in the sieve plate tower.
Mechanical Features
The Podbielniak contactor is a horizontally mounted centrifuge. The Pod has perforated, concentric cylindrical bands that fit into grooves on the rotor at one end and the endplate at the other. As seen in figure 3, the rigid inner shaft supports the rotor, and also provides the ports that serve as process liquid inlets and outlets. The shaft is drilled almost to the center from each side, but not through. There is a central channel and an annular channel on both the sides. This provides the four channels needed for process liquid flow.
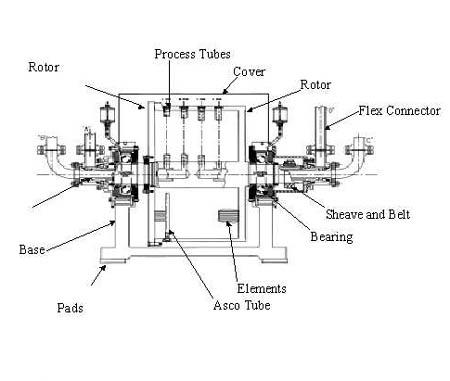
Feed tubes are provided inside the rotor for each inlet and outlet that connect to the shaft. These tubes extend to the rim and are drilled into the rotor for added stability. These tubes are cross-drilled at the appropriate radius to provide an inlet or outlet for a liquid. The unique mechanical design of the Pod offers the following features:
- Stability. Horizontal orientation provides increased stability compared to vertical centrifuges. This robust configuration makes the centrifuge more tolerant to vibrations caused by process upsets. The rotor is supported by widely spaced bearings, which also increases stability. The bearings are oversized due to flow requirements, providing a L10 bearing life of greater than 100,000 hours. Low operating RPM compared to other centrifuges leads to longer life of rotating parts.
- Hermetic. The Pod is flooded with the process liquids during operation. The Pod is equipped with mechanical seals in order to facilitate hermetic operation. As the Pod is flooded with process liquids at all times, internal volume usage is maximized.
- Ease of Operation. Podbielniak contactors are automated by the use of a variable frequency drive. The only mechanical monitoring required is for speed, lubrication flow for the bearings and product flow for wetting of the mechanical seals. Once the Pod is up and running, it requires minimal supervision.
- Versatility. The elements are customized for each application, taking into consideration variables like flow rates, percentage and properties of solids in feed, viscosity of material, etc. The Pod elements can be tailored for systems with solids in order to minimize the solids buildup, reducing downtime due to cleanup. Some feed tubes can be removed from the rim, which provides access to the inside of the rotor for cleanup without disassembly. To accommodate for corrosive materials, the Pod has been manufactured out of alloys such as Hastelloy C, Monel, Inconel, Alloy 20, etc.
Principles of Operation
As seen in figure 4, the heavy liquid (HLI) is introduced near the shaft, and the light
liquid (LLI) is introduced near the rim of the rotor. As a result of the centrifugal force and density difference, the heavy liquid is forced out to the rim. As the heavy liquid propagates through the perforations, it displaces an equal volume of light liquid towards the shaft. The two liquids flowing countercurrently are forced to pass each other through the perforations on each band, leading to intense contact. The light liquid is collected at the shaft (LLO), and the heavy liquid is collected at the rim (HLO). This countercurrent series of dispersion and coalescence allows multi-stage extraction.
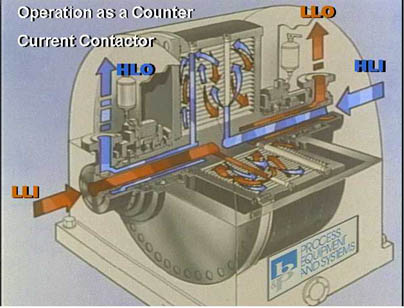
The internal volume of the Pod is divided into three cylindrical zones based on the radial position of the two liquid inlets. The countercurrent contact zone is the volume enclosed between the two inlet radii. In this zone, the two liquids are forced countercurrently through the perforations leading to intimate contact and maximum surface area generation for mass transfer.
Inboard of the contact zone is light liquid clarification zone, where the light liquid is settled and entrained heavy liquid is removed. Similarly, the heavy liquid clarification zone, which is outboard of the contacting zone, clarifies the heavy liquid before it exits the Pod.
Process Feasibility
The criteria for process feasibility in a Pod are that the two liquids are at least partially immiscible and have a density difference. If the two liquids are totally miscible, they cannot be physically separated. In addition, the flow streams should not have more than 30 to 40% (v/v) solids. The Pod extractor is manufactured in the various sizes, with capacities ranging from 0.4 GPM for the A-1 model test unit to as high as 600 GPM for the E-48. The capacities are derated for systems with solids, low density difference and viscous liquids.
Process Variables
The major variables involved with the Pod operation are pressures, flowrates and Xg force. The inlet pressures are constant and are a function of the rotor speed and density difference. The outlet pressures are variable and are used to control the quality of the effluent streams. The LLO pressure reflects the position of the major interface inside the Pod, which allows dispersion of a selected liquid into the other in order to maximize interfacial surface area for mass transfer.
The flow rate ratio and cumulative flow rate can be varied to optimize a Pod extraction process. As the amount of solvent used (in other words, the flow rate ratio) is increased, the degree of extraction increases as well. Theoretically, the maximum dispersion of the two liquids is performed when all the trays in the contact zone are operating near flooding levels. As a rule of thumb, the Pod is operated at a cumulative flow rate around 85% of flooding rate, so that there is some room for fluctuation in feed conditions.
The Xg force, which is a function of RPM, dictates the maximum flow rate that the Pod can handle. The Xg force can be increased to provide additional separation force. The Xg force can be reduced at lower flow rates to operate the Pod at close to flooding conditions in order to get better extraction. Other variables that can affect an extraction process are feed conditions like concentration and temperature.
Limitations
Many Pod applications involve process liquids with some solids, which tend to build up on elements over time. This decreases effective internal volume, and ultimately decreasing extraction and separation efficiency. These solids have to be physically or
chemically removed, and require a shutdown of the process. This limits the Pod to applications with less than 40% solids volumetrically. The operating time between shutdowns and total down time vary on the nature and amount of solids in the feed. In addition, the Pod capacity is derated for viscous materials, as the resistance to the flow of liquids is increased.
Advantages
Robust mechanical features along with distinctive process design make the Pod a unique contactor for extraction and separation. The Pod is a differential countercurrent centrifugal extractor, (opposed to the batch-wise countercurrent configuration in mixer-settlers and most centrifuges) which increases extraction efficiency at a given flow rate ratio. Internal clarification zones allow handling of easily emulsified systems resulting in both effluent streams that are free of entrainment in most cases. The unique design of the Pod reduces solvent usage and operating costs while producing better product at higher yields in a safer environment.
The hermetic design allows complete enclosure of process fluids, resulting in these benefits:
- Safer operation with hazardous solvents due to complete enclosure
- Reduces the possibility of product contamination
- Prevents oxidation or degradation of product by avoiding contact with air
- Solvent and product losses are minimized
The Pod has a small rotor volume compared to mixer-settlers and extraction columns, which offers the following advantages:
- Relatively high capacities due to multiple Xg force and generation of large amount of interfacial area in a small geometric space
- Small rotor and high flow rate leads to short residence time – important when product degenerates at extraction conditions
- Reduces capital investment required when costly material of construction is required
- Small footprint enables the rotor to be added to just about any existing plant
The unique Pod design offers the following distinct advantages over other liquid-liquid
extraction centrifuges:
- Horizontal orientation, resulting in increased stability
- Combination of Xg force along with low shear inside the Pod, reducing the possibility of emulsion formation
- Separation of liquids with specific gravity gradient as low as 0.01
- Mechanical seals allowing any permutation of the process liquids in order to provide safest handling of the materials involved. Hazardous solvents are passed across the inner seals so that accidental leaks to atmosphere are prevented
- As the fluids enter and leave at the same axial position, the liquids do not lose potential energy in the centrifugal field. Hence, power requirements are low as only external windage and internal friction needs to be overcome.
Applications
Due to its unique design, the Pod has been successfully used in hundreds of applications, ranging from lube oil extraction to vaccine production. There are three main types of applications: extraction, separation and simultaneous separation with countercurrent wash. Extraction constitutes the majority of Pod applications, with up to five theoretical stages extracted in a single unit.
In pharmaceuticals, the Pod has been used to extract antibiotics such as penicillin, erythromycin, and tylosin. The Pod has also been used in biological applications, including hormone and vitamin extraction and food processes like edible oil processing and citrus flavor extraction.
One of the Pod's first applications, in 1945, was the extraction of penicillin. Generally, two Pods are used in countercurrent series, giving a 90-95% extraction efficiency at a broth to solvent ratio of 2:1. Filtered broth results in 98% extraction at a broth to solvent ratio of 4:1. The hermetic design along with short contact time in the Pod enables mass production of penicillin, as it degrades over time at extraction conditions.
Chemical
The Pod has worked well in applications where an organic product stream is purified by reacting the impurities out using an acid or a caustic wash. The Pod has been used for many applications like acrylics, aromatics, fumaric acid, plasticizer refining, polycarbonate washing, insecticide and herbicide manufacturing, acid and caustic treating of lube oil, etc.
For example, in plasticizer refining tricresyl phosphate is countercurrently contacted with a mild caustic solution at a 1:1 ratio to remove acidic impurities like phenols and cresols. The intermediate product is then contacted with wash water countercurrently in the second Pod at a 1:1 flow ratio to wash out the salts. The acidic impurities are decreased from 0.5-1% to 0.03-0.07%.
Liquid ion exchange, where cations or anions are exchanged between two liquids, involves a chemical reaction between the product and the ion exchanger in the organic solvent. Hence, the reaction kinetics governs the extraction rather than surface area formation (as in most Pod applications). There are two steps in this process: Loading, when the solvent is loaded with the product, and stripping, where the product is extracted back into the aqueous phase. Liquid ion exchange applications such as hydrometallurgical extractions in mineral processing, citric acid, and waste dye extraction.
During waste dye extraction waste sulfonic acid dye is extracted from an aqueous waste stream via liquid ion exchange in the Pod. The loading step has an efficiency of 97% while using a 23:1 wastewater to solvent ratio. After passing through the stripping stage, the wastewater is concentrated volumetrically by a factor of 700. Hence, the generation of wastewater is drastically reduced. The solvent is recirculated in a closed loop.
Simultaneous Separation and Countercurrent Wash
This unique setup allows handling two process steps in one unit operation. A mixed feed is introduced through the LLI port. The two liquids are phase separated, and the lighter liquid moves towards the shaft. Water is introduced from the HLI port, which counter-currently washes out the exiting light liquid of any water-soluble impurities. The Pod has been utilized for such processes as naphthenic acid recovery, continuous soapstock acidulation, parrafin neutralization and washing, polyol washing, etc.
Food
Vegetable oil degumming is used to recover lecithin from unrefined oil. A mixture of oil and hydrated gums is introduced near the rim. The heated feed is mixed with 2-3% water or steam, which dissolves the lecithin out. 90% of the lecithin is removed from the oil using the Pod.
Other Promising Applications
Extensive research is going on to introduce the Pod into non-conventional, emerging separations such as:
- Supercritical fluid extraction, used in an increasing number of chemical, pharmaceutical, and food applications
- Phytosol extraction, developed by Advanced Phytonics, a UK-based R&D company. Typical applications include fragrance and flavor extraction, fermentation broth extraction, and wastewater treatment.
Summary
Unique processing capability along with robust mechanical design has made the Pod highly successful in hundreds of extraction and separation applications. With nearly one
thousand Pods built and used successfully, the future of the Pod looks even brighter as new and unconventional applications are on the horizon.
References
- Todd, D. B., Davies, G. R., Kaiser H. R. "Controlled Centrifugal Separation of Liquids", Third Symposium on Hazardous Chemicals Handling and Disposal, 1972.
- Todd, D. B., Davies, G. R. "Centrifugal Pharmaceutical Extraction", Filtration and Separation, November/December 1973.
- McHugh, M.A., Krukonis, V.J. "Supercritical Fluid Extraction: Principles and Practice", Butterworth-Heinemann Publications, Second Edition, 1994.
- Ruthven, D.M. "Encyclopedia of Separation Technology" Wiley Interscience, 1997.
- Perry, R. H., Green, D. W., "Perry's Chemical Engineer's Handbook", sixth edition, McGraw-Hill, 1984.
For more information: Gitesh Dubal, Process Engineer, B & P Process Equipment and Systems, LLC, 1000 Hess Ave., Saginaw, MI 48601. Tel: 517-757-1300. Fax: 517-757-1301.