New Developments In Passivation Technology
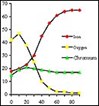
By John J. Kilkeary and Tim Sowell, N/A Corp.
Introduction
Better Passivation Formulations
Better Measurement Techniques
Future Results From Current Passivation Developments
Further Reading
Introduction (Back to Top)
In recent years, there has been a growing awareness of the importance of passivation in maintaining clean stainless steel vessel and piping surfaces. Passivation can be thought of as a specialized cleaning procedure in which "rustable" iron and other contaminants are removed from the surface to provide a chromium rich surface layer. This process makes iron less available at the surface to form iron oxides (rust or rouge) during operations.
If corrosion products are allowed to form then metal deterioration occurs and in some cases, product quality is adversely affected. Before reviewing the new developments in passivation technology it is important to understand the basic mechanisms of passivation. The most common construction material used in pharmaceutical processes is 316L stainless steel.
Table 1 shows the average composition of this material. As can be seen, the ratio of chrome to iron in the base metal is approximately 0.24.
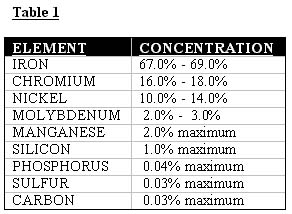
By chemically treating the surface of the stainless steel, such that iron is removed, then the ratio of chrome to iron is increased. With a good passivation procedure, elemental chrome to iron ratios in the range of 0.75 to 2.0 can be attained. Reducing iron content at the surface, while leaving chrome, results in a "chromium rich" surface which is less likely to form corrosion products. The "chromium rich" or passive layer is found to be extremely thin—not more than 50 angstroms in depth.
It is often thought that once a system has been passivated it will remain in this state forever. Unfortunately, the environments that are found in purified water and clean steam systems are extremely corrosive and the passive layer is under constant attack. The use of strong oxidizers in frequent sanitization processes also effect the passive layer thus bringing forth the migration of free iron at the surface.
With this continuous attack on the metal, it is imperative to know that the surface has been provided with the greatest possible corrosion resistant surface through a thorough cleaning and passivation treatment. There are several methods of testing for corrosion resistance and surface chemistry. We will cover these techniques and their practical use.
Before chemically treating the metal surface to achieve passivity, the metal surface is submitted to a "smoothing" or polishing operation for the purpose of reducing surface roughness. Reducing the surface roughness also reduces the surface area and the opportunity for bacterial growth to adhere to the stainless surface. This improvement in smoothness facilitates ease in Clean-In-Place (CIP) cleaning.
Commonly, "smoothing" is accomplished by means of electropolishing or mechanical polishing. Electropolishing (EP) is achieved by dipping the stainless steel in an electrolytic bath. The electrolytic solutions are typically mixed acids and organic additives, including sulfuric and phosphoric acid. EP is an electrochemical process which selectively removes metal to smooth the surface and reduce its area. This procedure "shaves" and removes the surface peaks—essentially the reverse of plating the surface.
Electropolishing is typically required for all pharmaceutical high purity tubing systems. This process can leave certain contaminants on the surface, like sulfates and phosphates, which must be removed prior to passivation. Stringent control of current and voltage are required to maintain proper EP.
Mechanical polishing and precision lapping can achieve a smooth surface by grinding off the metal peaks using abrasive media. Frequently, abrasive compounds such as aluminum oxide are left in the surface. Aluminum inclusions left in the surface layer can later lead to corrosion, if left untreated. Metal inclusions or contaminants can be specific sites for pitting corrosion. These contaminants need to be removed prior to passivation.
Until recently, the most common passivation procedure consisted of cleaning the surface with an alkaline cleaner and then passivating with nitric acid. Testing the surface with a color change technique known as the "Ferroxyl Test" as outlined in ASTM A380, checked the effectiveness of the procedure by indicating the presence of free iron at the surface. The problem with this method and chemistry is that is does not differentiate between a poorly passivated and well-passivated surface.
The ferroxyl test offers no quantitative data as to the amount of chromium oxide or iron at the surface. Aluminum inclusions are not indicated and can be specific sites of corrosion.
New developments in passivation technology have proceeded in two different areas. The first of these new developments is the improvement in chemistry for the removal of surface contaminants and the second is the employment of advanced instrumental techniques to measure the passive layer.
Better Passivation Formulations (Back to Top)
With the availability of improved measurement techniques, it became possible to develop better passivation formulations. The first step in the development process was to re-formulate passivation chemistry to replace the mineral acids (nitric or phosphoric) with organic acids (primarily citric and other chelant materials). These latter chemicals were able to selectively remove specific metal ions from the surface to prevent the hide out or masking of iron and enhance the chromium oxide layer. This selective process is based on the use of different chelants and the varying pH of the solutions. Not only does the chelant chemistry do a better job of rendering the surface contaminant free, but it also has the added advantage of safety in use and less costly disposal.
The second step in reformulation was to add to the base organic acids, other materials to enhance the free iron removal. As a result of the new formulation work, the best performing passivation fluids are formulations contain as many as five or six ingredients. The additional ingredients include surfactants, acid chelants that react with specific metals, buffer agents to maintain pH ranges and stronger reducing acids that assist in the dissolution of iron oxides. Stronger reducing agents and specific chelants improve the dissolution of higher temperature corrosion products (silica included) and metal oxide contaminants.
Better Measurement Techniques (Back to Top)
Ferroxyl testing can indicate the presence of iron particles, but it lacks the precision to differentiate between the effectiveness of the various passivation treatments. Three test methods, new to the practice of passivation, are now coming to the forefront. These test methods are AES (Auger Electron Spectroscopy), XPS (X-Ray Photoelectron Spectroscopy) or ESCA (Electron Spectroscopy for Chemical Analysis), and Cyclic Polarization (CP). Each process gives a more precise and analytic way to measure the degree of passivity.
Auger Electron Spectroscopy (AES)
This surface analysis technique bombards the metal surface with electrons. The difference between the elements' binding energy and the electron bombardment is a unique number which
identifies the element. The concentration of the element is related to the intensity of
the peak. AES can be used as a scan across the surface, or it can also be used to analyze deeper into the steel by using it with an argon ion-sputtering gun.
Using this instrument, you can determine the relative amounts of chrome to iron at each level of depth. Figures 1 and 2 show the element tracings from a non-passivated and a passivated metal sample. Note that the peak chrome to iron ratio is approximately 1.0 in the electropolished non-passivated sample. Upon passivation, this same metal showed a maximum chrome to iron ratio of nearly 2.0. This doubling of the chrome to iron ratio indicates a significant increase in the surface corrosion resistance.
X-Ray Photoelectron Spectroscopy (XPS)
The XPS (or ESCA, Electron Spectroscopy for Chemical Analysis) is very similar to AUGER Spectroscopy. Again, the surface is bombarded, but in this technique, X-Rays are used. In addition, a larger effected area is vaporized from the metal surface (50 angstroms depth and 200 angstroms across). The instrument can not only determine elemental chrome to iron ratios but also chromium oxide to iron oxide ratios and provide information about what chemical form (oxidation state) the various elements have taken.
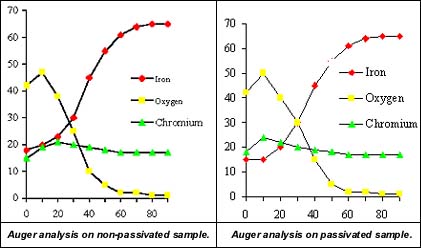
Cyclic Polarization
While AES and ESCA techniques give indications of relative corrosion resistance by analyzing chemical composition, the Cyclic Polarization (CP) is an electrochemical test (ASTM-G61) that measures the point at which pitting corrosion begins. CP uses an electrolytic cell to directly measure the corrosion rate. By using the test piece as the working electrode, initiation of localized corrosion is shown by the potential at which the current density increases rapidly. This point is call the "pitting potential." The lower the current density at this point, the more resistance to pitting corrosion. The current density is measured in micro-amps per square centimeter.
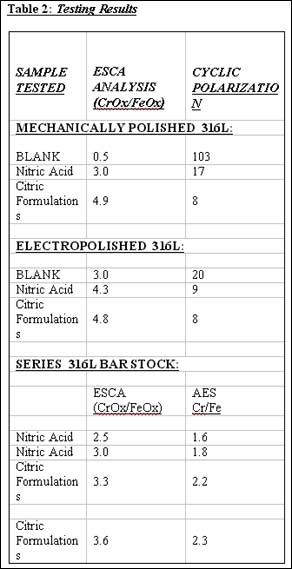
Several research investigations were undertaken to determine if the citric/chelant formulations were as good or better than the traditional nitric acid treatments. Both electropolished and mechanical polished samples were prepared and treated. All metal samples were cut from the same lot of 316L stainless steel. Duplicate samples were prepared and then submitted for testing by the ESCA method and also by the CP technique. Results of the tests are summarized in Table 2. The citric formulations proved equal or better than the nitric acid passivation procedures with each of the three measurement techniques. Of note is the significant improvement found in the corrosion resistance of the electropolished samples with the use of either passivation technique.
A second series of tests were run on samples of 316L bar stock material and designed to compare nitric passivation and citric chelant passivation techniques. The results for AES and ESCA tests are also listed in Table 2. All these tests show the improvement in the passive layer with the chelant treatments.
Future Results From Current Passivation Developments (Back to Top)
Several practical outcomes will result from current efforts to bring more science into the passivation practice.
- Passivation formulations will continue to improve as new instrumental techniques are employed to select the best products.
- End users will have a reliable, objective way to determine if a thorough passivation has been performed.
- The validation professionals will have meaningful passivation measurements for their certification documents.
- Direct measurement of corrosion rates will assist future treatment design and scheduling of maintenance.
All these efforts will move us closer to the goal of "rust free" operations in pharmaceutical facilities.
Banes, P. Fundamentals of passivation in water systems. Ultrapure Water,
April, 1998 P. 60
Balmer & Larter. Chelants prove practical for cleaning and passivation of stainless
steel parts. Precision Cleaning Dec. 1994.
Henon, B., Pitting potentials of passivated and unpassivated orbitally welded 316L
tube samples. Process Piping Symposium Univ. of Wisconsin, March 1998.
Coleman & Evans. Fundamentals of Passivation in the Pharmaceutical Industry. Pharmaceutical Eng. March 1990.
Roll, D. Current Methodologies Used in Passivation Procedures. Proceedings
InterPhex Pharmaceuticals Conference, April 1996.
For more information: John J. Kilkeary, Astro Pak Corp., 1936 National Ave., San Diego, CA 92113. Tel: 619-231-1022. Fax: 619- 231-0575.